What is sand blasting
- Wilson Pipeline
- Jan 4, 2022
- 11 min read
What is sand blasting?
Sand blasting is a surface treatment process that uses compressed air as power to form a high-speed jet beam to spray sand at high speed to the workpiece surface to be treated. The compressed air is used as the power to form a high-speed jet beam to spray the sprayed materials (copper ore, quartz sand, emery, iron sand and steel sand) to the workpiece surface to be treated at high speed, so as to change the appearance or shape of the outer surface of the workpiece surface. Due to the impact and cutting effect of abrasive on the workpiece surface, the workpiece surface can obtain certain cleanliness and different roughness, The mechanical properties of the workpiece surface are improved, so the fatigue resistance of the workpiece is improved, the adhesion between it and the coating is increased, the durability of the coating film is prolonged, and it is also conducive to the leveling and decoration of the coating.
Sand blasting can remove all dirt such as rust on the surface of the workpiece, and establish a very important foundation on the surface of the workpiece (usually the so-called rough surface). Moreover, it can achieve different degrees of roughness by exchanging abrasives with different particle sizes, greatly improve the adhesion between the workpiece and coatings and plating, or make the bonding parts more firm and better quality.
Sand blasting process
Sand blasting process is dry sand blasting. The abrasives can be steel sand, alumina, quartz sand, silicon carbide, etc., but quartz sand is the most widely used in China. Abrasives of different substances can be selected according to the requirements of part materials, surface conditions and processing.
Dry sand blasting process conditions for different parts
Part type
Degree of quartz sand (mm)
Compressed air pressure (MPA)
Large steel parts with thickness over 3 mm.
2.5~3.5
0.3~0.5
Medium sized steel parts with thickness of 1 ~ 3mm.
1.0~2.0
0.2~0.4
Small thin brass parts.
0.5~1.0
0.15~0.25
Steel sheet metal parts and aluminum alloy parts with thickness less than 1 mm.
0.5 ~ down
0.1~0.15
There are two kinds of dry sand blasting: mechanical sand blasting and air pressure sand blasting. Each method is pided into manual, non automatic or continuous automatic modes. Manual air pressure sand blasting machine is widely used in China, and it also uses various complex shapes of small and medium-sized parts.
Wet spray Sand technology
The abrasive used in wet sand blasting is the same as that of dry sand blasting. The abrasive can be mixed with water to form mortar. The abrasive is usually 20% – 35% and stirred continuously to prevent sinking. Compressed air is used to press into the nozzle and sprayed to the parts. Sand and water can be put into the tank respectively and mixed before flowing to the nozzle before spraying to the parts. In order to prevent corrosion of steel parts, sodium nitrite and other corrosion inhibitors must be added in water, Sand should be dried before next use.
There are many kinds of equipment for wet sand blasting machine, and the most commonly used one is sand blasting chamber.
Spray Pill Technology
(1) General On
Shot peening is similar to sand blasting, but steel shot or glass shot is used instead of abrasive for sand blasting. Shot peening can produce compressive stress on parts, and there is no dust pollution containing silicon. This process is mainly used for:
(1) The fatigue strength and stress corrosion resistance of the parts are improved by compressive stress.
(2) Straighten the twisted thin-walled parts.
(3) Instead of the general cold and hot forming process, the large thin-walled aluminum parts are processed, which can avoid the high residual on the surface of the parts Tensile stress And the favorable compressive stress is formed.
It should be noted that the service temperature of the parts after shot peening should not be too high, otherwise, the compressive stress will be eliminated and the expected effect will be lost. The limit of using temperature depends on the material of the parts. For example, the temperature of steel parts is about 260 ~ 290 ℃, and that of aluminum parts is about 170 ℃.
(2) Types of pills
1. Cast steel shot: its hardness is generally 40-50HRC. When processing hardware metal, the hardness can be increased to 57-62HRC. Cast steel shot has good toughness and is widely used. Its service life is several times that of cast iron shot.
2. Cast iron shot: its hardness is 58-65HRC. It is brittle and easy to be broken. It has short life and is not widely used. It is mainly used in occasions with high strength without shot peening.
3. Glass pill: hardness is lower than the former two, mainly used in stainless steel. Titanium, aluminum, magnesium and other materials that do not allow iron contamination can also be used for secondary processing after shot peening to remove iron contamination and reduce surface roughness of parts.
(3) Shot blasting technology
For shot peening, which requires compressive stress on the surface of parts, it must have enough coverage, which is difficult.
In addition, it is difficult to make quantitative judgment. Therefore, the method of controlling shot peening strength is often adopted, that is, the method requiring a certain sandblasting degree is required, that is, the required stress value can be obtained after reaching a certain sandblasting strength. The shot peening strength is mostly in accordance with the American SAE standard J442.
Almen arc altimeter was used for measurement
Almen arc height meter uses 1070 cold rolled steel with thickness of 0.8 mm, 1.3 mm or 2.4 mm. Compared with 70 carbon steel in China, its hardness is 44-50 HRC. The shot peening strength can be obtained by measuring the arc height of bent steel bar. The shot peening strength is mainly affected by the following factors:
(1) Shot size: the larger the shot peening, the greater the impact energy, the greater the shot peening intensity, and the shot peening coverage. Therefore, on the premise of producing the required shot peening strength, it is beneficial to reduce the shot size as much as possible.
In addition, the selection of shot peening size is also limited by the shape of shot peening parts, and its diameter should not exceed half of the radius of the inner circle of the groove. The particle size of shot peening is generally 2.00-0.30mm
(2) Hardness of Shot Peening: when the hardness is greater than the hardness of parts, the change of shot peening hardness value does not affect the shot peening strength, otherwise, the decrease of shot peening hardness will reduce the shot peening strength.
(3) Shot peening speed: when the shot peening speed is increased, the shot peening intensity will be increased, but if the shot peening speed is too high, the crushing amount will increase.
(4) Spray angle: when it is vertical, the shot peening intensity is the highest. Therefore, shot peening is generally carried out in this state. If it is necessary to peen at a small angle due to the shape of the parts, the size and speed of shot peening shall be appropriately increased.
(5) Shot peening fragmentation: the shot peening strength of crushing shot blasting is low, so the shot peening should be removed frequently to ensure that the integrity of shot peening is not less than 85%. In addition, the shot with sharp angle will scratch the parts.
Function and application of sand blasting
(1) Pretreatment of workpiece coating and workpiece bonding
Sand blasting can remove all dirt such as rust on the workpiece surface, and establish a very important basic schema (commonly known as rough surface) on the workpiece surface. Moreover, it can achieve different degrees of roughness by exchanging abrasives with different particle sizes, such as flying abrasives and abrasives of abrasives, so as to greatly improve the binding force between the workpiece and coatings and plating materials. Or make the bonding parts bond more firmly and have better quality.
(2) Cleaning and polishing of casting rough surface and workpiece after heat treatment
Sand blasting can clean all dirt (such as oxide scale, oil stain and other residues) on the surface of castings and forgings and workpieces after heat treatment, polish the surface of workpieces, improve the smoothness of workpieces, expose uniform and consistent metal color, and make the appearance of workpieces more beautiful and good-looking.
(3) Burr cleaning and surface beautification of machined parts
Sand blasting can clean the micro burrs on the workpiece surface, make the workpiece surface more flat, eliminate the harm of burrs and improve the grade of the workpiece. And sand blasting can make a small fillet at the junction of the workpiece surface, making the workpiece more beautiful and more precise.
(4) Improve the mechanical properties of parts, mechanical parts
After sandblasting, uniform and fine concave convex surfaces can be generated on the surface of parts to store lubricating oil, so as to improve lubrication conditions, reduce noise and improve mechanical service life.
(5) Gloss effect
For some special purpose workpieces, sandblasting can realize different reflection or matte at will. Such as the polishing of stainless steel workpieces and plastics, the polishing of jade, the matte surface of wooden furniture, the pattern pattern on the surface of frosted glass, and the texturing of cloth surface.
▲ the left is the effect after sandblasting
Sand blasting is the most thorough, universal, rapid and efficient cleaning method. Sand blasting treatment can be arbitrarily selected between different roughness, but other processes cannot achieve this. Manual grinding can make rough surface, but the speed is too slow. Chemical solvent cleaning is too smooth, which is not conducive to coating bonding.
Type of sand blasting machine
Sand blasting machine is the most widely used product of abrasive jet. Sand blasting machine is generally pided into dry sand blasting machine and liquid sand blasting machine. Dry sand blasting machine can be pided into suction type and press in type.
Suction dry sand blasting machine
1. General composition
A complete suction dry sand blasting machine is generally composed of six systems, namely structure system, medium power system, pipeline system, dust removal system, control system and auxiliary system.
2. Working principle
The suction dry sand blasting machine is powered by compressed air and forms a negative pressure in the spray gun through the high-speed movement of air flow. The abrasive is sucked into the spray gun through the sand conveying pipe, shot out through the nozzle and sprayed to the machined surface to achieve the expected processing purpose. In the suction dry sand blasting machine, compressed air is not only the feeding power, but also the accelerating power.
Press in dry sand blasting machine
1. General composition
The working unit of a complete press in dry sand blasting machine is generally composed of four systems, namely pressure tank, medium power system, pipeline system and control system.
2. Working principle of press in dry sand blasting machine.
The press in dry sand blasting machine is powered by compressed air. Through the working pressure established in the pressure tank by compressed air, the abrasive is pressed into the sand conveying pipe through the sand discharge valve, shot out through the nozzle, and sprayed onto the machined surface to achieve the expected machining purpose. In the press in dry sand blasting machine, compressed air is not only the feeding power, but also the accelerating power.
Liquid sand blasting machine
Compared with dry sand blasting machine, the biggest feature of liquid sand blasting machine is to well control the dust pollution in the process of sand blasting and improve the working environment of sand blasting operation.
1. General composition
A complete liquid sand blasting machine is generally composed of five systems, namely structure system, medium power system, pipeline system, control system and auxiliary system.
2. Working principle
The liquid sand blasting machine takes the grinding fluid pump as the feeding power of the grinding fluid, and the evenly stirred grinding fluid (mixture of abrasive and water) is transported to the spray gun through the grinding fluid pump. As the acceleration power of grinding fluid, compressed air enters the spray gun through the gas transmission pipe. In the spray gun, compressed air accelerates the grinding fluid entering the spray gun, and shoots out through the nozzle to the machined surface to achieve the expected processing purpose. In the liquid sand blasting machine, the grinding liquid pump is the feeding power and the compressed air is the accelerating power.
Grade of sand blasting
That is, cleanliness. There are two representative international standards: one is “SSPC -” formulated by the United States in 85; The second is “SA -” formulated by Sweden in 76. It is pided into four levels: SA1, SA2, Sa2.5 and SA3. It is an international common standard. The details are as follows:
SA1 – equivalent to sspc-sp7 in the United States. The general simple manual brushing and abrasive cloth grinding methods are adopted, which is the lowest level of the four kinds of cleanliness, and the protection of the coating is only slightly better than that of the untreated workpiece. Technical standard for SA1 treatment: the workpiece surface shall be free of oil, grease, residual oxide scale, rust spots, residual paint and other dirt. Grade SA1 is also called manual brushing and cleaning grade( Or cleaning level).
SA2 – equivalent to SSPC-SP6 in the United States. Sand blasting is the lowest level of sand blasting, that is, general requirements, but the protection of the coating is much higher than manual brushing. Technical standard for SA2 level treatment: the workpiece surface shall be free of greasy, dirt, oxide scale, rust scale, paint, oxide, corrosion and other foreign substances (except defects), but the defects shall not exceed 33% per square meter of surface, including slight shadows; A small amount of slight discoloration caused by defects and corrosion; Oxide scale and paint defects. If there is a dent on the original surface of the workpiece, slight rust and paint will remain at the bottom of the dent. SA2 grade is also called commodity cleaning grade (or industrial grade).
Sa2.5 level – it is widely used in industry and can be used as the acceptance technical requirements and standards. Sa2.5 level is also called near white cleaning level (near white level or out of white level). Technical standard for Sa2.5 treatment: the same as the first half of SA2 requirements, but the defects are limited to no more than 5% per square meter of surface, including slight shadow; A small amount of slight discoloration caused by defects and corrosion; Oxide scale and paint defects.
SA3 – equivalent to sspc-sp5 in the United States, is the highest treatment level in the industry, also known as white cleaning level (or white level). Technical standard for SA3 treatment: the same as Sa2.5, but 5% of shadows, defects, rust, etc. shall not exist.
Sandblasting raw materials
Sand blasting: that is to spray the pattern part into a very fine frosted surface with metal sand particles of different sizes and models on the production mold of gold and silver coins. When producing gold and silver coins, a layer of beautiful silver appears in the pattern part, which increases the sense of three-dimensional and hierarchy.

Refined quartz sand
Quartz sand, ordinary quartz sand and refined quartz sand for sand blasting (refer to derusting or plating on metal surface): high hardness, good derusting effect, and physical and chemical indexes are as follows:
SiO2 ≥ 88-99.8% Fe2O3 ≤ 0.1-0.005%, fire resistance 1450-1800 ℃, uniform appearance particles, common particle sizes of 1-3mm and 0.1-0.3mm, pure white. The particle size range is mostly 5-220 mesh, which can be produced according to the user’s requirements. Main uses: metallurgy, ink, silicon carbide, glass and glass products, enamel, cast steel, water filtration, bubble alkali, chemical industry, sand blasting and other industries.
Sandblasting rubber hose: the inner and outer rubber of sandblasting pipes are usually made of wear-resistant materials, mostly NBR (acrylonitrile butadiene copolymer), SBR (oil filled styrene butadiene rubber), or there is a kind of paralubber (clover rubber) with better service performance of imported hose. The common wear resistance coefficient is 60 ~ 75 cubic mm.
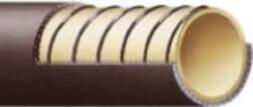
Operating procedures for sand blasting
Wear protective equipment before work, and do not work with bare arms. At least two people shall work.
The air storage tank, pressure gauge and safety valve shall be calibrated regularly. The air storage tank discharges dust every two weeks, and the filter in the sand tank is checked once a month.
Check whether the ventilation pipe and sandblasting machine door are sealed. Five minutes before work, the ventilation and dust removal equipment must be started. When the ventilation and dust removal equipment fails, the sand blasting machine is prohibited to work.
The compressed air valve shall be opened slowly, and the air pressure shall not exceed 0.8MPa.
The sand blasting particle size shall adapt to the work requirements, generally between No. 10 and No. 20, and the sand shall be kept dry.
When the sand blasting machine is working, irrelevant personnel are not allowed to approach. When cleaning and adjusting the operating parts, stop the machine.
Do not blow dust or joke with compressed air.
After work, the ventilation and dust removal equipment shall continue to operate for five minutes and then shut down to discharge indoor dust and keep the site clean.
In case of personal and equipment accidents, the site shall be protected and reported to relevant departments.
Comments