What is a breather valve?
- Wilson Pipeline
- Jan 5, 2022
- 12 min read
What is a breather valve?
Breather valve is a kind of valve which can not only keep the tank space isolated from the atmosphere within a certain pressure range, but also connect with the atmosphere (breathing) when the pressure range is higher or lower. Its function is to prevent the tank from being damaged due to overpressure or vacuum, and to reduce the evaporation loss of the storage liquid. It is mainly composed of valve seat, valve cover, protective cover and two groups of opening and closing devices controlled by vacuum and pressure. The opening and closing device includes valve disc, guide rod, spring, spring seat and sealing ring. When the pressure in the tank reaches the rated exhaled positive pressure, the pressure valve flap opens and the steam in the tank is discharged; when the vacuum degree in the tank reaches the rated suction negative pressure, the vacuum valve flap opens and the air enters.
Structure characteristics of breather valve
The breather valve is made of cast iron, cast steel, aluminum alloy and stainless steel with good corrosion resistance.
The valve disc and seal ring are made of stainless steel tetrafluoroethylene.
The breather valve has good low temperature resistance and antifreeze performance.
The breather valve is a ventilation device installed on the fixed roof tank to reduce the evaporation loss of oil and control the pressure of the tank.
The breather valve has the advantages of large ventilation, small leakage, corrosion resistance and good antifreeze performance. It can automatically adjust the pressure inside and outside the oil tank.
Function of breather valve
The internal structure of the breather valve is essentially a combination of a pressure valve disc (that is, an exhalation valve) and a vacuum valve disc (that is, an inhalation valve). The pressure valve disc and the vacuum valve disc can be arranged side by side or overlapped.
The working principle of the breather valve is that when the pressure in the tank reaches the rated positive exhalation pressure, the pressure valve flap opens and the vapor in the tank is discharged; when the vacuum in the tank reaches the rated suction negative pressure, the vacuum valve flap opens and air enters.
1. When the pressure of the medium in the tank is within the control operating pressure range of the breather valve, the breather valve does not work to maintain the tightness of the oil tank;
2. When the medium is added to the tank to increase the pressure in the upper gas space of the tank and reach the positive operating pressure of the breather valve, the pressure valve is opened and the gas escapes from the breather valve exhalation outlet, so that the pressure in the tank does not continue increase; as shown in the figure below:
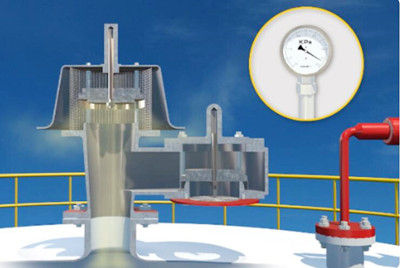
3. The atmosphere outside the tank will open the negative pressure valve disc of the breather valve and suck in air; as shown in the figure below:

The breather valve plays a sealing role under normal conditions. It can only work under the following conditions:
(1) When the storage tank outputs materials, the breather valve begins to suck air or nitrogen into the tank.
(2) When the material is filled into the tank, the breather valve starts to exhale the gas from the tank to the outside.
(3) Due to climate change and other reasons, the vapor pressure of materials in the tank increases or decreases, and the breather valve exhales steam or inhales air or nitrogen (usually called thermal effect).
(4) In case of fire, the evaporation of liquid in the tank increases sharply due to the heat of exhaled gas, and the breather valve begins to exhale out of the tank, so as to avoid the damage of the tank due to overpressure.
(5) In other working conditions, such as the pressurized transportation of volatile liquid, chemical reaction of internal and external heat transfer devices, misoperation, etc., the breather valve will exhale or inhale accordingly, so as to avoid damage to the storage tank due to overpressure or ultra vacuum.
Working principle of breather valve
The internal structure of the breather valve is essentially composed of a pressure valve disc (i.e. exhalation valve) and a vacuum valve disc (i.e. suction valve). The pressure valve disc and vacuum valve disc can be arranged side by side or overlapped. Its working principle: when the pressure of the tank is equal to the atmospheric pressure, the disc and seat of the pressure valve and vacuum valve are closely matched, and the sealing structure on the side of the seat has “adsorption” effect, so that the seat is tight without leakage. When the pressure or vacuum degree increases, the valve disc starts to open, because there is still “adsorption” effect on the seat edge, so it can still maintain a good seal.
When the pressure in the tank rises to the constant value, the pressure valve is opened, and the gas in the tank is discharged into the outside atmosphere through the exhalation valve (pressure valve). At this time, the vacuum valve is closed due to the positive pressure in the tank. On the contrary, when the pressure in the tank drops to a certain degree of vacuum, the vacuum valve opens due to the positive pressure of atmospheric pressure, and the external gas enters the tank through the suction valve (i.e. vacuum valve), and the pressure valve is closed.
At any time, the pressure valve and vacuum valve cannot be opened at the same time. When the pressure or vacuum in the tank drops to the normal operating pressure, the pressure valve and vacuum valve are closed, and the process of exhalation or inhalation is stopped.
Common standards for Breather valves
Commonly used standards for Breather valves are:
SY/T 0511.1-2010 “Petroleum Storage Tank Accessories Part 1: Breather valve”
TB/T 3319-2013 “Breathing safety valve for railway tank car”
QC/T 1064-2017 “Tank Vehicle Breather valve for Road Transport of Flammable Liquid and Dangerous Goods”
DIN EN 14595-2016 “Dangerous Goods Transport Tank, Tank Operating Device Pressure and Vacuum Breather valve”
Classification of breather valve
Tight breather valve
The tight breather valve is usually used in low-pressure straight-through pipelines. The sealing performance depends entirely on the goodness of the fit between the plug and the plug body. The compression of its sealing surface is achieved by tightening the lower nut. Generally used for PN≤0.6Mpa.
Packed breather valve
Packing type breather valve realizes the sealing of plug and plug body by pressing the packing. Due to the packing, the sealing performance is better. Usually, this kind of breather valve has a packing gland, and the plug does not need to extend out of the valve body, thus reducing a leakage path of the working medium. This kind of breather valve is widely used for the pressure of PN≤1Mpa.
Self-sealing breather valve
The self-sealing breather valve realizes the compression and sealing between the plug and the plug body through the pressure of the medium itself. The small head of the stopper extends upwards out of the body, and the medium enters the big head of the stopper through the small hole at the entrance to press the stopper upwards. This structure is generally used for air medium.
Oil-sealed breather valve
The scope of application of breather valves continues to expand, and oil-sealed breather valves with forced lubrication appear. Due to forced lubrication, an oil film is formed between the plug and the sealing surface of the plug body. In this way, the sealing performance is better, the opening and closing is labor-saving, and the sealing surface is prevented from being damaged.
Classified by material
Cast iron breather valve, carbon steel breather valve, cast steel breather valve, stainless steel (304, 304L, 316, 316L) breather valve, aluminum alloy breather valve, plastic (PVC, PP) breather valve;
Classified by working principle
The first is to exhale or inhale when a certain pressure is reached; the other is designed to only exhale but not inhale, which can be understood as replacing it with two check valves with appropriate pressure.
The second type of breather valve is similar to a one-way check valve. It can only breathe out, not inhale. When the pressure in the system rises, the gas will pass through the breather valve to vent outwards to ensure a constant pressure in the system. For storage tanks that store toxic substances, there is no breather valve, and treatment devices such as activated carbon filters can be added.
breather valves are generally used on normal pressure or low pressure storage tanks, that is, only normal pressure and low pressure storage tanks have breather discharge (the low pressure tank often has a steam recovery system), and the high pressure storage tank has no discharge, no breather loss and work loss .
The main emissions of fixed roof tanks are pided into breather loss (small breather discharge) and work loss (large breather discharge).
Installation of Breather valve
1. Remove the packaging, it is very important to read the product description.
2. When hoisting the breather valve, appropriate lifting tools should be used to avoid damage to the protective cap of the breather valve disc.
3. Check the coaxiality and verticality of the pipe flange on the tank or water tank, which is essential for the normal use of the pressure and vacuum relief valve (Breather valve).
4. Check the waterline surface of the pipe flange on the tank or water tank. It must be clean, free of scratches, corrosion, tool marks, and flat.
5. Remove the flange port protection cover and other packing materials.
6. Check the gasket; make sure the material is suitable for the application.
7. Use the bolt circle to center the washer.
Installation points of Breather valve
(1) The Breather valve should be installed at the highest point on the top of the tank. Theoretically speaking, from the viewpoint of reducing evaporation loss and other exhaust gas, the breather valve should be installed at the highest point of the gas phase space of the tank in order to smoothly provide the most direct and largest passage to the breather valve.
(2) When the volume of the storage tank is large or the storage tank is more important, in order to prevent the risk of overpressure or negative pressure in the storage tank due to failure of a single Breather valve, two Breather valves can be installed at this time. In order to avoid two Breather valves operating at the same time and increasing the probability of failure, during process design, the suction and discharge pressure gradients of the two Breather valves are usually designed. Normally, the next one works and the other is standby.
(3) If the breather volume is too large and the breather volume of a single Breather valve cannot meet the requirements, more than two Breather valves can be set. When installing two Breather valves, their distance from the center of the tank top should be equal, that is, they are arranged symmetrically on the tank top.
(4) If the breather valve is installed on a nitrogen-sealed storage tank, the position of the nitrogen gas supply pipe must be far away from the breather valve interface and inserted into the storage tank from the top of the tank for about 200mm, so that the nitrogen is not directly discharged after entering the tank. Nitrogen sealing effect.
(5) If there is a flame arrestor in the breather valve, the influence of the pressure drop of the flame arrestor on the discharge pressure of the breather valve must be considered to avoid overpressure in the storage tank.
(6) When the average temperature of the coldest month in the tank building area is lower than or equal to 0, the breather valve must have anti-freezing measures to prevent freezing or blocking of the breather valve valve disc, resulting in poor exhaust or insufficient air supply of the storage tank , Which leads to overpressure drum or low pressure deflated tank.
Breathing discharge calculation of breather valve
The respiratory emissions of the fixed roof tank can be estimated by the following formula:
LB=0.191×M(P/(100910-P))^0.68×D^1.73×H^0.51×△T^0.45×FP×C×KC
In the formula:
LB-respiratory discharge volume of fixed top tank (Kg/a);
M-the molecular weight of the vapor in the tank;
P-In a large amount of liquid state, the true vapor pressure (Pa);
D-The diameter of the tank (m);
H-average vapor space height (m);
△T- the average temperature difference within a day (℃);
FP-coating factor (dimensionless), the value is between 1 and 1.5 according to the paint condition;
C-Adjustment factor for small diameter tanks (dimensionless); For tanks with a diameter between 0-9m, C=1-0.0123(D-9)^2; C=1 for tanks with a diameter greater than 9m;
KC-product factor (Petroleum crude oil KC is 0.65, other organic liquids are 1.0).
Working discharge calculation of Breather valve
Work emissions are losses due to man-made loading and unloading. As a result of charging, when the pressure in the tank exceeds the release pressure, the vapor is forced out of the tank; while the discharge loss occurs when the liquid is discharged, and the air is drawn into the tank, and the air becomes a gas saturated with organic vapor and expands. Therefore, the capacity of the vapor space is exceeded.
The working emissions of the fixed roof tank can be estimated by the following formula:
LW=4.188×10^-7×M×P×KN×KC
In the formula:
LW-Work loss of fixed roof tank (Kg/m3 input);
KN-Turnover factor (dimensionless), the value is determined by the number of annual turnover (K).
Turnover times=annual input/tank capacity
K<=36,KN=1
36
K>220, KN=0.26
Pressure test of Breather valve
1. Test preparation
Install the fire-stop Breather valve on the test bench correctly, the device should not leak, and the inner wall of the test tube should be flat and smooth.
2. Detection medium
The detection medium for the opening pressure, ventilation and leakage of the fire resistance Breather valve is air, the absolute pressure is 0.1Mpa, the temperature is 20℃, the relative humidity is 50%, and the density is 1.2kg/m3. If the air is not in this state, Should be converted to gas in this state. The detection medium for the pressure of the flame retardant Breather valve body is 5-35 ℃ clean water.
3. Air pressure detection
First detect its leakage, and then detect its sensitivity and ventilation volume one by one.
4. Water pressure detection
The water pressure test of the fire retardant Breather valve is 0.2Mpa, and the pressure holding time is 10min.
5. Pressure detection
Install the fire-resistance Breather valve on the connecting flange of the gas storage tank, adjust the valve to gradually increase or decrease the pressure in the gas storage tank, adjust the valve disc to make it open, and read from the connected micromanometer Output the pressure value, read the value once every minute, and then rotate the valve disc by 90° and 180° respectively, repeat the above test, repeat each working condition three times, and take the average value.
6. Leakage detection
The leak detection pressure is 0.75 times the operating pressure, and this value is read on the micromanometer. The value of the leakage is read from the flowmeter (the accuracy of the flowmeter is 0.5-1.0 level). Read each measurement value once per minute for a total of three readings, and take the average.
7. Low temperature detection fire resistance Breather valve. Install the fire resistance Breather valve on the test frame and put it in the low temperature box. The temperature in the low temperature box will drop to 4-15℃, and the continuous input relative temperature of the low temperature box should not be less than 70%. The air at room temperature reaches the end of the breather valve before the end of the valve disc is opened, and then the temperature in the low temperature box is reduced to -30 ℃, after 24 hours of constant temperature, connect one side of the test frame to the micromanometer, and the other side passes through A surge tank containing room temperature air is connected to the aerodynamic force. When the valve disc of the breather valve is in the open state, read the pressure value. repeat three times.
Maintenance of Breather valve
The Breather valve is maintained and maintained once a month and twice a month in winter. The method: first slightly open the valve cover, take out the vacuum valve disc and the pressure valve disc, check the valve disc and valve disc seal, valve disc guide rod and guide rod sleeve for oil and dirt, such as oil and dirt The objects should be cleaned up, then put back in place, and pull up and down a few times to check whether the opening is flexible and reliable. If everything is normal, then tighten the valve cover. In the maintenance and maintenance, if there is any abnormal phenomenon such as scratches or wear on the valve disc, it should be replaced immediately or contact the supplier company to solve it in time.
Breather valve selection should first follow the four principles of safety, reliability, applicability, and economy in sequence, and then follow the six aspects of on-site working conditions (namely, pipeline parameters, fluid parameters, pressure parameters, action methods, and special requirements). select).
The following factors are mainly considered when selecting the breather valve:
1. For the requirements of the installation location and temperature range, such as cold areas, all-weather Breather valves should be used, and pipeline breather valves should be used for installation in pipelines.
2. The control pressure of the mechanical Breather valve should be compatible with the relevant pressure bearing capacity.
3. The specifications (flange diameter) of the mechanical Breather valve should meet the requirements of the maximum flow rate of breather gas in and out of the oil tank.
4. Consider the exhalation volume caused by the increase in the evaporation of liquid in the tube caused by the heating of the tank during a fire.
5. Under the influence of climate, the increase of vapor pressure in the tank decreases, resulting in the thermal effect of breather.
6. Anti-freeze Breather valve should be selected for selection in northern cold regions.
7. The maximum amount of liquid in and out of the tank.
First, determine the breather volume of the breather valve according to the working conditions of the specific occasions where the breather valve is set up and the prescribed calculation method or formula, and then select the breather valve according to the various specified performance curves of different constant pressure values provided by the breather valve manufacturer size. It also determines the take-off pressure and ventilation pressure of the breather valve. When a single breather volume cannot meet the requirements, more than two Breather valves can be set.
Confirm the minimum pressure of the vessel design and the maximum allowable pressure of the vessel, that is, the determination of negative pressure and positive pressure, and the operating pressure range.
Source: China Valves Manufacturer – wilsonpipeline Pipe Industry Co., Limited (www.wilsonpipeline.com)
Commentaires