Welding Technology of Natural Gas Pipeline
- Wilson Pipeline
- Jan 5, 2022
- 7 min read
Natural gas pipeline refers to the pipeline that transports natural gas (including associated gas produced in oil field) from the production site or treatment plant to urban gas distribution center or industrial enterprise users, also known as gas transmission pipeline. Using natural gas pipeline to transport natural gas is a way to transport natural gas on land. Natural gas pipelines account for about half of the world’s total pipelines. China’s modern natural gas pipeline industry is mostly concentrated in Sichuan Province, the main natural gas producing area. In 1963, the first Bayu gas transmission pipeline with a diameter of 426 mm and a total length of 54.7 km was completed. By 1983, it had built a gas transmission pipeline network from east Sichuan to Chengdu, Deyang and other places through Chongqing, Luzhou, Weiyuan, etc., with a diameter of 426-720mm, a total length of more than 2200km, 178 gas gathering and distribution stations and an annual capacity of 5-6 billion cubic meters. In addition, in Daqing, Shengli, North China and other oilfields, there are pipelines to transport associated gas to petrochemical plants.
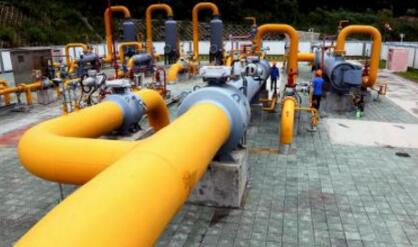
Welding Technology of Natural Gas Pipeline
I. Universal Welding Method
Generally, semi-automatic welding is the main method of Engineering welding, and manual arc welding downward welding can be used for locally difficult sections and joints. The downward welding operation rules must conform to the stipulations of the Downward Welding Procedure Regulations for Pipelines.
1. AWS_E6010 cellulose electrode is used for manual arc welding, AWS_E8010 electrode is used for filling, and AWS_E8018G low hydrogen electrode is used for cap.
2. Semi-automatic root welding adopts AWS_E6010 electrode, filling and capping adopts E71T8-Ni1 or 71T8-K6 flux cored wire.
II. Welders
1. Establish a welding quality management system according to the welding process before construction. Train and test the welders according to the requirements of the welding process approved by the owner, so that the technical quality and technical level of the welders can meet the relevant regulations of the construction acceptance criteria of this project.
2. All welders participating in the construction of this project must have the “Welder Qualification Certificate” issued by the State General Administration of Technical Supervision or the provincial and municipal technical supervision bureaus and the “Work Certificate” issued by the pre-job supervisor, so as to hold the certificate to work.
III. Major Welding Equipment
Power supply: Semi-automatic welding power supply is DZ-80 mobile power station produced by Pipeline Machinery Equipment Company. The power station is equipped with DC-400 Lincoln multi-system welding machine, which can meet manual welding at the same time.
IV. GENERAL REQUIREMENTS
1. Pipeline welding with X70 material needs preheating before welding. Ring heater and baking handle are used for preheating. Pre-heating width: the groove on both sides (> 50mm), preheating temperature, interlayer heating temperature: according to the temperature specified in the welding procedure for heating treatment. The preheating temperature is measured by infrared thermometer 50 mm away from the pipe orifice.
There is no preheating requirement for other materials.
2. The arc initiation or closure of weld beads are staggered for more than 30 mm. Welding arc initiation is carried out in groove, and arc initiation on groove outside welding layer is not allowed, let alone on pipe wall outside groove. Every arc-starting point and joint must be repaired before welding. After the first welding layer is completed, the next welding layer is started.
3. After the root welding is completed, angular polishing machine is used to grind and clean up the slag, spatter, defects and weld protrusion on the outer surface of the root welding. The groove shape on the outer surface of the pipe shall not be damaged by grinding, and the time interval between root welding and filling shall not exceed 10 minutes.
4. All beads should be welded continuously and the interlayer temperature of beads should meet the required requirements. After the weld is finished, the splash and slag on the surface of the joint must be cleaned up. Before the completion of the weld bead on that day, more than 50% of the whole weld bead should be completed at each weld joint and not less than three layers. In welding construction, the “welding process record” should be filled in carefully according to the regulations.
5. Dry, waterproof and heat-insulating materials should be used to cover the unwelded joints on that day. Before welding the next day, the temperature required by the welding procedure should be preheated. For the unused welding wire on the same day, the wire feeder should be removed from the wire feeder or put together with the wire feeder into the warehouse equipped with dehumidifier at the construction site for dehumidification treatment. The next day after arriving at the construction site, immediately remove the tape wrapped on the pipe mouth, grind the root, and then use the annular heater to heat the left mouth. The heating temperature requirements are the same as the temperature of the pipe mouth group. The heating quality must be approved by the on-site supervision engineer.
6. In the welding process, the rubber protective layer with a width of 800mm is wound around the two ends of the anti-corrosion layer to prevent welding splash and burn.
7. Welding material requirements
(1) Each batch of welding materials must have a certificate of quality, a certificate of conformity and a report of reexamination. Imported materials should also have a certificate of commodity inspection.
(2) The appearance of welding materials should be smooth, clean, crack-free, rust-free, oil and other contaminants.
(3) Welding materials are strictly prohibited from being eroded by dampness, rainwater and oil. They should be stored in dry and ventilated rooms with humidity less than 60%.
(4) The shelf of welding material is more than 300 mm above ground, more than 300 mm away from wall, and the stacking height does not exceed the specified number of layers.
(5) Damage to welding materials and packaging should be avoided during storage and handling. After opening the package, it should be protected from deterioration. Welding materials with signs of damage or deterioration should not be used in engineering.
(6) Set up a special person to keep and distribute welding materials, and make good records of distribution and recovery, meteorological records and baking records.
(7) When using the electrode, it should be placed in the barrel of the electrode. When the relative humidity of the environment is greater than 80%, the usage of the electrode should be limited for two hours, and when the relative humidity of the environment is less than 80%, the usage of the electrode should be limited for four hours.
(8) The unused electrodes on that day shall be retrieved and stored. Low hydrogen type electrode should be used first after re-drying, and the number of re-drying should not exceed two times.
(9) Each electrode should be welded continuously, and the welder should avoid the occurrence of arc breaking as far as possible.
(10) Welding wire can not be dried. It should be stored in a dry and ventilated room and kept dry.
(11) If the eccentricity of the electrode is large, the coating cracks, dropping and other phenomena affecting the welding quality, they shall not be used for welding.
(12) After the completion of welding, the remaining electrodes shall not be discarded at will, and special persons shall be responsible for recovery and centralized treatment.
V. Welding Environment
Welding is strictly prohibited in the following cases, such as without effective protective measures (such as shelter, heater, etc.).
When the wind speed exceeds the requirements of the welding procedure, special windshield shall be provided to ensure the sealing requirements of the welding site.
When the ambient wind speed affects the welding operation, effective wind-proof measures should be taken to protect the welding area. According to the past construction experience, we usually adopt the method of wind-proof.
Ⅵ. Welding inspection
1. Visual inspection
After welding, repair or repair, visual inspection shall be carried out in time. Before inspection, slag, splash and other dirt on the surface shall be removed. The weld appearance shall meet the acceptance standard specified in welding and acceptance of steel pipeline. Non destructive testing shall not be carried out for welds that fail to pass the visual inspection. The weld appearance inspection shall meet the following requirements.
(1) The appearance of the weld is uniform, and the surface of the weld and its heat affected zone shall be free of defects such as cracks, lack of fusion, air holes, slag inclusions, splashes, clamp welds, etc
(2) The weld surface shall not be lower than the base metal surface, and the weld reinforcement shall not be greater than 1.6mm.
(3) The width of each side of the weld surface shall be 0.5-2mm wider than the groove surface.
(4) The unfitness after welding shall be less than 2mm
(5) The maximum size of undercut shall meet the requirements.
(6) The arc burn mark shall be polished off, and the remaining pipe wall thickness shall not be reduced less than the minimum thickness allowed by the material standard after grinding. Otherwise, the whole section of the pipe with arc burn mark shall be cut off.
2. Non destructive testing of welds
All butt welds shall be subject to 100% radiographic testing, and the ultrasonic testing retest (commonly known as double hundred testing) shall be conducted according to the following requirements. The design requirements are to test according to the actual requirements:
(1) Perform 100% ut on the following welds:
a. All pipe joints in class III and class IV areas;
b. Pipeline welded junction crossing large and medium-sized rivers, mountain tunnels, swamps, reservoirs, highways and railways above class III;
c. Pipeline welded junction crossing underground pipeline, cable and optical cable;
d. Welded junction of straight pipe and elbow;
e. Butt weld after sectional pressure test;
f. The first 100 welds initially welded by each unit;
(2) After 100% radiographic inspection, 10% of all welded joints completed on the same day of each unit shall be subject to ultrasonic flaw detection: the unqualified welded joints shall be repaired as required, and the defect repair times of the same part shall not exceed 1, and the repaired parts shall be subject to 100% ultrasonic re inspection.
Ⅶ. Repair
1. The non crack defects in the weld bead can be repaired directly. If the repair process is different from the original welding process, the qualified repair welding process must be used.
2. When the crack length is less than 8% of the weld length, the qualified repair welding procedure shall be used for repair. When the crack length is more than 8%, all welds with cracks must be cut off from the pipeline.
3. The repair times of defects in the same part shall not exceed 1 time, otherwise the weld shall be cut off. After repair, test according to the original standard.
Source: China Natural Gas Pipelines Manufacturer – wilsonpipeline Pipe Industry Co., Limited (www.wilsonpipeline.com)
Comentarios