Selection of stainless steel for handling nitric acid (HNO3)
- Wilson Pipeline
- Jan 5, 2022
- 2 min read
Nitric acid is strongly oxidising and promotes the resistance of stainless steel to corrosion. Generally stainless steel are resistant to corrosion in nitric acid. Nitric acid is used in the chemical passivation of stainless steel.
Commercially concentrated acid is around 65 wt % (sg = 1.40). Higher concentrations obtained by removing water, which can involve the use of sulphuric acid, which has a high affinity for water.
Corrosion resistance of stainless steel
Nitric acid is strongly oxidising and attacks most metals but due to its powerful oxidising nature, it promotes the resistance of stainless steel to corrosion. Generally stainless steel are resistant to corrosion in nitric acid over a wide range of concentration and temperature. The ‘helpful’ oxidising properties of nitric acid are used in the chemical passivation of stainless steel.
The iso-corrosion diagram 0.1mm/year lines for the 304 and 316 types coincide (purple).
(The broken line represents the boiling point)
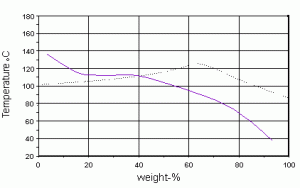
This shows that the 304 types can be used over a wide range of concentration and temperature, up to 95%, for storage applications. The 304 types are preferable to 316 types for nitric acid applications however. This is an exception to the ‘general rule’ for stainless steels where the 316 types are normally found to be more corrosion resistant than 304 types.
Over 95% concentration, aluminium alloys should be considered OR 4% silicon stainless steels.
Any additional chlorides or fluorides in nitric acid may increase corrosion rates by pitting.
Risk of localised corrosion in concentrated acids
Localised attack at grain boundaries (IC) can occur in hot concentrated nitric acid.
This can occur in the heat-affected-zone (HAZ) of welds. Prolonged heating in a range of around 600-800 degC, followed by exposure to concentrated nitric acid, can also result in localised attack, due to the precipitation of the brittle “intermetallic” (iron-chromium) compounds (sigma phase).
Avoiding localised attack in concentrated acid
To avoid the risk of localised corrosion, especially where post weld heat treatment is impractical, the low carbon, 304L types should be considered. Solution heat treatment (1050 -1100 degC followed by fast cooling) on the standard carbon 304 types can be considered as an alternative. These treatments should also re-dissolve any sigma formed.
Compostions of 304L types have been used with silicon, phosphorous & sulphur limited to very low residual levels to improve the resistance in hot concentrated nitric acid.
Uses for nitric acid with stainless steels
Nitric acid is widely used in the chemical ‘passivation’ of stainless steels.
Source: wilsonpipeline Pipe Industry Co., Limited (www.wilsonpipeline.com)
Comments