Sealing principle and characteristics of flat welding flange
- Wilson Pipeline
- Jan 5, 2022
- 6 min read
A flat welded flange is a type of flange that is joined to a vessel or pipe by a fillet weld. It is an arbitrary type of flange. According to the degree of integrity of the connection between the flange ring and the straight section, the design is checked according to the integral or loose flange. The flange ring is available in both neck and neck. Compared with the neck-welded flange, the flat-welded flange has a simple structure and is material-saving, but the joint is not as good as the neck-welded flange. Flat welded flanges are widely used in the connection of medium and low pressure vessels and pipes.
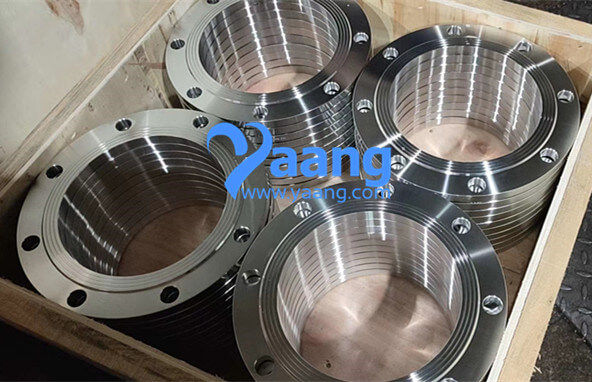
Flat welding flange features:
The flat welded flange not only saves space, reduces weight, but more importantly ensures that the joint is not leaked and has good sealing performance. The reduced size of the compact flange is due to the reduced diameter of the seal which will reduce the cross-section of the seal face. Second, the flange gasket has been replaced by a seal ring to ensure that the seal faces the sealing surface. In this way, only a small amount of pressure is required in order to press the cover tightly. As the required pressure is reduced, the size and required number of bolts can be reduced accordingly, so a new design that is small in size and light in weight (70% to 80% lighter than conventional flanges) is designed. product. Therefore, the flat welding flange type is a relatively high quality flange product, which reduces the quality and space and plays an important role in industrial use.
The sealing problem of the flat welding flange has always been a hot issue related to the production cost or economic benefit of the enterprise, so the sealing principle of the flat welding flange has been improved and improved. However, the main design defect of the flat welding flange is that it can not be leak proof. This is a defect in design: the connection is dynamic and periodic loads, such as thermal expansion and fluctuating loads, will cause mutual movement of flange faces, affect the function of the flange, thus damage the integrity of the flange, and eventually lead to leakage.
No product can be free of defects, but try to minimize the defects of the product, so the company improves the performance of the product as much as possible and plays the largest role in the production of flat welding flange.
Sealing principle of flat welding flange:
The two sealing faces of the bolt squeeze the flange gasket to form a seal, but this can also cause seal damage. In order to keep the seal, you have to maintain a large bolt force, in order to do this, you have to make the bolt larger. Larger bolts match larger nuts, which means larger bolt diameters are needed to create the conditions for tightening the nuts. However, the larger the bolt diameter, the flange will be bent, the only way is to increase the wall thickness of the flange part.
The sealing problem of the flat welding flange has always been a hot issue related to the production cost or economic benefit of the enterprise, so the sealing principle of the flat welding flange has been improved and improved. However, the main design defect of the flat welding flange is that it can not be leak proof. This is a defect in design: the connection is dynamic and periodic loads, such as thermal expansion and fluctuating loads, will cause mutual movement of flange faces, affect the function of the flange, thus damage the integrity of the flange, and eventually lead to leakage.
No product can be free of defects, but try to minimize the defects of the product, so the company improves the performance of the product as much as possible and plays the largest role in the production of flat welding flange. Features of flat welding flange: flat welding flange not only saves space and weight, but also ensures no leakage at the joint and good sealing performance. By reducing the seal diameter, the size of the compact flange is reduced, so the seal section is reduced.
Secondly, replace the flange gasket with a sealing ring to ensure that the confidential cover matches the sealing surface. In this way, the sealing surface can be tightened with only a small amount of pressure. With the decrease of the required pressure, the size and quantity of the bolts are reduced accordingly. Therefore, a new product with small volume and light weight is designed, which can reduce the weight of the traditional flange by 70% ー 80%. Therefore, the plate welding flange is a relatively high-quality flange product, which reduces the quality and space, and plays an important role in the industrial application.
The two sealing faces of the bolt squeeze the flange gasket to form a seal, but this can also cause seal damage. In order to keep the seal, you have to maintain a large bolt force, in order to do this, you have to make the bolt larger. Larger bolts match larger nuts, which means larger bolt diameters are needed to create the conditions for tightening the nuts. However, the larger the bolt diameter, the flange will be bent, the only way is to increase the wall thickness of the flange part.
Common production process for flat welding flange
Round forging process of round steel pure material;
Finished forging and cutting forming process;
Steel plate cutting and blanking processing technology;
Rough forging, expansion machine thermal expansion production process;
Steel plate rolling production process, generally for large diameter flanges, such as flanges above DN600;
The above is the type of flange raw material production process, but high-precision CNC lathe turning, CNC rocker drilling, final flange forming, packaging workshop for flange printing stencil marking and packaging, the company quality inspection department to carry out inspection, The inspection report is issued and the final flange is taken out of the warehouse. Forging of flat welded flanges can be pided into free forging, upsetting, extrusion, die forging, closed die forging, and closed upsetting. Closed die forging and closed upset forging have high material utilization due to the absence of flash. Finishing of complex forgings is possible with one or several processes. Since there is no flash, the area of force applied to the forging is reduced and the required load is also reduced. However, care should be taken not to completely limit the blank. To this end, the volume of the blank is strictly controlled, the relative position of the forging die is controlled, and the forging is measured to reduce the wear of the forging die. According to the movement mode of the forging die, the flat welding flange can be pided into pendulum, pendulum swivel, roll forging, cross wedge rolling, boring ring and cross rolling. Swing, swivel and shackle can also be used for precision forging. In order to improve the utilization of materials, roll forging and cross rolling can be used as a front-end process for slender materials. The same rotary forging as free forging is also partially formed, which has the advantage that it can be formed in the case of a smaller forging force than the forging size. In this forging method including free forging, the material expands from the vicinity of the mold surface to the free surface during processing. Therefore, it is difficult to ensure the accuracy of the flat welding flange. Therefore, the moving direction of the forging die and the swaging process are controlled by a computer. flat welding flanges can be used to obtain products with complex shapes and high precision with low forging force.
Flat welding flange connection application
The smooth flat welding flange is the most widely used. The flat welded steel flange is suitable for the nominal pressure not exceeding 2.5MPa. The carbon steel pipe connection. The sealing surface of the flat welding flange can be made smooth. It is more suitable for medium conditions. In the case, such as low-pressure non-purified compressed air and low-pressure circulating water, the advantage is that the price is relatively cheap. The structure is reasonable, and the welded steel flange is used for the opposite welding of the flange and the pipe. The strength and rigidity are large, and the high temperature can withstand. High pressure and repeated bending and temperature fluctuations, reliable sealing. Nominal pressure is 0.25 2.5MPa. The butt welding flange adopts concave and convex sealing surface.
The flat welding flange gasket is placed between the two flange sealing surfaces. After tightening the nut, the specific pressure on the surface of the gasket reaches a certain value and then deforms, and fills the unevenness on the sealing surface, so that the joint is tight. A flanged joint is a detachable joint. There are holes in the flange, bolts can be worn to make the two flanges tightly connected, and the flanges are sealed with gaskets. According to the connected parts, it can be pided into container flange and pipe flange.
flat welding flanges are often used when the medium temperature and pressure are not high and the medium is corrosive. When the medium is corrosive. Rare integral flanges have flat and butt weld flanges. Flange fittings are flanged (flange or splicing) fittings. It can be cast, and the flat welded flange is mainly a part that connects the pipe and the pipe to each other. According to the structure type. It can also be constructed by screwing or welding. Flange joints consist of a pair of flanges, a gasket and a number of bolts and nuts.
Source: China Flat Welding Flanges Manufacturer – wilsonpipeline Pipe Industry Co., Limited (www.wilsonpipeline.com)
Comentários