Main factors affecting flange sealing performance
- Wilson Pipeline
- Jan 4, 2022
- 6 min read
Bolt pre-tightening force
An important factor affecting sealing. The pre-tightening force must compress the gasket to achieve the initial seal. Properly increasing the bolt pre-tightening force can increase the sealing ability of the gasket, because increasing the pre-tightening force can make the gasket retain a larger contact surface pressure under normal working conditions.
However, the pre-tightening force should not be too large, otherwise the gasket will yield as a whole and lose its resilience, or even extrude or crush the gasket. In addition, the preload should be applied to the gasket as evenly as possible. Measures are usually taken to reduce the bolt diameter, increase the number of bolts, and take appropriate pre-tightening methods to improve the sealing performance.
Gasket performance
The gasket is an important component of the seal. The function of the gasket is to seal the gap between the sealing surfaces of the two flanges and prevent fluid leakage. The types of gaskets include non-metal gaskets, non-metal and metal combination gaskets and metal gaskets.
Appropriate gasket material requires that the gasket can produce the necessary elastic deformation under the action of appropriate pre-tightening force without being crushed or squeezed out; the distance between the flange sealing surface is increased during operation, and the gasket material should It has sufficient resilience to keep the gasket surface in close contact with the flange surface to continue to maintain good sealing performance;
The working medium and working temperature should also be considered when selecting gasket materials. The width of the gasket is also an important factor affecting the seal. The wider the gasket, the greater the pre-tightening force required, and the larger the size of bolts and flanges is required.
① Non-metallic gaskets such as rubber, asbestos rubber, polytetrafluoroethylene, etc. are commonly used on medium and low pressure equipment and pipeline flanges. They have good corrosion resistance and flexibility, but their strength and temperature resistance are poor. They are usually cut from the entire gasket sheet. The shape of the entire gasket is a ring with a rectangular cross section.
② In order to improve the strength and heat resistance of the gasket, thin steel belts and asbestos belts (or PTFE belts or flexible graphite belts) are wound together to form spiral wound gaskets, or asbestos or other non-metallic materials are wrapped with metal sheets made of metal-clad gaskets have multiple sealing effects and good resilience. They are used in higher temperature and pressure ranges, and can maintain good sealing under pressure and temperature fluctuations, so they are widely used.
Spiral wound gaskets are made by winding steel belts with asbestos, polytetrafluoroethylene or flexible graphite and other filling belts. To prevent looseness, weld the beginning and end of the metal strip. In order to increase the elasticity and resilience of the gasket, both the metal strip and the non-metal strip are rolled into a wave shape. There are two wave shapes: V-shaped and W-shaped. There are 4 types of V-shaped structures.
Type A-also known as basic type, without reinforcement ring, used for tongue and groove sealing surface.
Type B-with inner strengthening ring for concave and convex sealing surface.
Type C-with outer reinforcement ring for flat sealing surface.
Type D–there are reinforced rings inside and outside for flat sealing surfaces.
③ The metal cladding gasket is made of asbestos rubber sheet as the inner core, and the outer thickness is 0.2~0.5mm thick thin metal plate (as shown below).

The material of the metal plate can be aluminum, steel and its alloys, stainless steel or high-quality carbon steel. Metal-clad gaskets are also only used on flanges of Type B flat welding and long-neck butt welding.
④ Metal gaskets are commonly used on flanges of high-pressure equipment and pipelines. The materials include soft aluminum, copper, mild steel and stainless steel. In addition to metal gaskets with rectangular cross-sections, there are also metal ring gaskets with elliptical or octagonal cross-sectional shapes and other special shapes.
When the operating pressure is very high or the leakage rate is very strict, and the temperature is very high or the corrosiveness is very strong, metal gaskets can be used. The specific pressure value of the metal gasket is very large. In order to reduce the bolt force, the pressing surface must be very narrow, relying on the extremely narrow pressing surface to maintain a good seal, and must have a small surface roughness, Ra≤2.5μm to Ra ≤0.63μm.
Types of sealing surface
The contact surface where the gasket is inserted between the flanges and pressed to achieve a sealing effect is called the flange sealing surface or the pressing surface. The selection of the sealing surface type is related to the operating conditions, the consequences of leakage and the nature of the gasket. The common structure types are as follows.
① Flat sealing surface: Its structure is shown in the figure (a) below. The sealing surface is not a smooth plane. There are often 2 to 4 concentric triangular cross-section grooves (ie flange waterline) on the plane. The flat sealing surface has a simple structure, is convenient to manufacture, and is convenient for anti-corrosion lining. Secondly, the width of the sealing surface of this structure is large, so non-metal or metal soft gaskets are often used in use. But after the bolts are tightened, the gasket material is easy to stretch to both sides. Used in occasions where the required pressing force is not high and the medium is non-toxic.
② Concave-convex sealing surface: The structure of the sealing surface is shown in the figure (b) below. It is equivalent to a pair of flat sealing surface flanges, one of which is made as a pressing surface with a raised platform, and the flange is called a convex flange, and the other correspondingly made concave is called a concave flange. The gasket with the same size as the concave is embedded in it, and the gasket is easy to center. The height of the convex plane is slightly greater than the depth of the concave surface, and it is tightly pressed with bolts to play a sealing role. This structure can limit the radial deformation of the gasket, prevent the gasket from being extruded, and improve the sealing performance to a certain extent. Suitable for occasions with higher pressure.
③ Tongue and groove sealing surface: in the middle of a pair of flat sealing surfaces in the width direction, one is made into a cross-section like a tenon, and the other cross-section is like a groove. The pressing surface is paired, as shown in the following figure (c), the former is called a tenon surface flange, the latter is called groove flange. The groove-shaped pressing surface can limit the radial deformation of the embedded gasket, with good sealing performance, and the gasket can be less eroded and corroded by the medium. But the tenon part is easy to damage. It is often used in flammable, explosive, toxic media and higher pressure occasions.
In addition, there are trapezoidal groove sealing surfaces and tapered sealing surfaces. The former uses an elliptical cross-section annular metal gasket, and the latter uses a lens-type annular metal gasket. The above two structures are forced sealing, which are commonly used on high-pressure pipelines.
The form and surface properties of the flange sealing surface play a vital role in the influence of the sealing effect. The flatness of the flange sealing surface and the perpendicularity between the sealing surface and the flange centerline directly affect the uniformity of the gasket force and the good contact between the gasket and the flange.
The roughness of the flange sealing surface should match the gasket requirements. Radial knife marks or scratches on the surface are not allowed, let alone surface cracks.
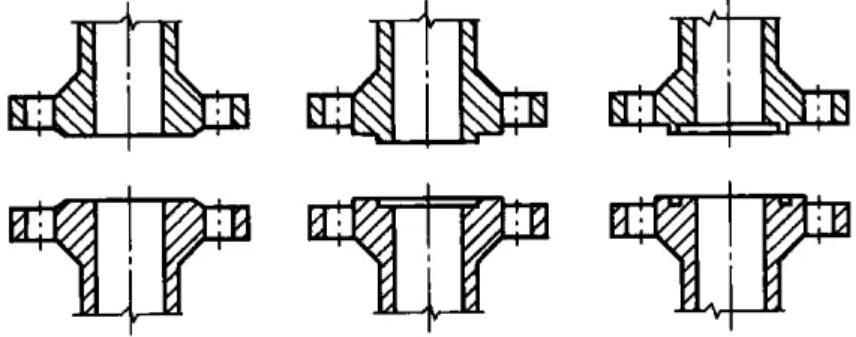
Flange stiffness
Excessive warpage due to insufficient flange rigidity (as shown in the figure below) is often one of the main reasons for the failure of the bolt flange connection seal in actual production. A flange with a large rigidity is small in deformation, and the bolt pre-tightening force can be evenly transmitted to the gasket, thereby improving the sealing performance of the flange.

The rigidity of the flange is related to many factors. Appropriately increasing the thickness of the flange ring, reducing the diameter of the bolt center circle and increasing the outer diameter of the flange ring can increase the rigidity of the flange. Use a necked flange or increase the size of the tapered neck part. , Can significantly improve the bending resistance of the flange. However, if the rigidity of the flange is increased without principle, the flange will become bulky and the cost will increase.
Operating conditions
The influence of pressure, temperature and the physical and chemical properties of the medium on the sealing performance is very complicated. The influence of pure pressure and medium on the sealing is not significant, but under the combined action of temperature, especially under fluctuating high temperatures, it will seriously affect the sealing performance , and even make the seal completely fail due to fatigue.
Because at high temperatures, the viscosity of the medium is small, the permeability is large, and it is easy to leak; the corrosive effect of the medium on gaskets and flanges is intensified, increasing the possibility of leakage; flanges, bolts and gaskets will all produce greater high temperatures creep and stress relaxation make the seal ineffective; certain non-metallic gaskets will also accelerate aging, deterioration, and even burn.
Source: China China Gaskets Manufacturer – wilsonpipeline Pipe Industry Co., Limited (www.wilsonpipeline.com)
Comments