Installation process and complete construction operation process of natural gas pipeline
- Wilson Pipeline
- Jan 5, 2022
- 14 min read
Installation process and complete construction operation process of natural gas pipeline
The installation and construction of natural gas pipeline includes three steps: pipeline welding, pipeline anti-corrosion and pipeline pressure test.
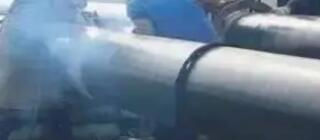
Survey site
According to the design and construction technical disclosure, the site survey shall be carried out jointly with the owner, supervision engineer and other relevant personnel.
Preparation before construction
1. Organize all construction personnel to conduct detailed investigation on other pipelines within the site and draw detailed construction sketches to ensure construction safety.
2. Check the performance indexes of the pipes used.
3. Cooperate with the on-site construction team, including pipe welding, pressurization and air tightness test.
4. The placement of equipment shall be considered from many aspects, that is, to facilitate construction and minimize the impact on the surrounding environment.
Surveying and setting out
According to the comparison between the design drawings and the site, accurately measure, point and mark the design pipeline position, and find and eliminate the obstacles that may affect the construction as early as possible.
Steel pipe derusting, anti-corrosion and painting
1. Before steel pipe welding, the oxide layer and dirt on the inner and outer pipe walls shall be removed. The derusting shall be carried out by electric polishing machine. The derusted pipes shall be painted with primer in time to prevent secondary oxidation.
2. The steel pipe adopts ordinary anti-corrosion, primer → finish coat → finish coat. Before anti-corrosion and painting of the steel pipe, the dirt such as rust, welding slag, burr, oil and water on the coated surface shall be removed. The coating shall be complete and uniform, the color shall be consistent, and there shall be no damage and flow; The coating film shall be firmly attached and the color shall be consistent.
Pipe welding
Steel pipe welding process requirements
1. The steel pipe should be cut by mechanical method. If it is cut by oxygen or acetylene flame, the size must be correct, the surface must be flat, and the notch shall be free of crack, double skin, burr, oxide, etc. Mechanical method should be adopted for groove processing to polish the uneven parts.
2. For pipe connection, it is not allowed to eliminate the gap, deviation, staggered joint and non concentricity of the pipe section by means of strong matching or heating the pipe. During alignment, the balance shall be measured 200mm away from the grounding center, and the allowable deviation is 2mm.
3. The inclination deviation of the cut end face shall not be greater than 1% of the outer diameter of the pipe and shall not exceed 3mm.
4. Pipe welding process:
(1) Material requirements: the material and specification must meet the design requirements, with factory certificate and retest report.
(2) Welding rod requirements: the coating shall be free of cracks, pores and other defects. During welding, the arc shall burn stably, melt evenly, and there shall be no blocking and falling off. It shall be dried for use.
(3) Preparation before welding: the pipe orifice shall be cleaned, the inner wall shall be flush, the misalignment shall not be greater than 1mm, the welded junction device shall be firm, and necessary measures shall be taken to prevent stress deformation during welding.
(4) Welding equipment: AC welding machine, DC welding machine, angle grinder, drying box and insulation barrel.
(5) Welder requirements: Welders must hold welding certificates and undergo pre job training and assessment. Safety protection shall be provided at the operation site to prevent burns, electric shock and collapse.
(6) Welding process: rust shall be removed before welding, and antirust paint shall be applied after exposing the natural color of the metal. During pipeline welding, reasonable welding methods and sequences shall be adopted to ensure the quality of arc starting and arc ending. Multi layer welded joints shall be staggered, and slag and spatter shall be removed after each layer is welded. If there is any defect, angular grinder shall be used to eliminate and re weld. Single side manual arc welding shall be used for welding, and after each welding is completed The first layer shall be polished with hand grinding wheel before welding the next layer. In order to reduce welding deformation and welding stress, symmetrical or segmented welding methods can be adopted. The welds shall be visually inspected. The weld reinforcement height shall be 1mm and the weld width shall cover the groove by 2mm. The weld surface shall be free of cracks: seams, pores and slag inclusion. The welds shall meet the 100% qualification of grade II films.
(7) Welding parameters:Pipe wall thickness (mm)Number of welding layersDiameter of electrodeWelding current (A)3.5-823.2105-120Name of the connectorPipe wall thickness (mm)Blunt edgeGroove angleHi-LoV-groove3-3.50-330º1
(8) Welding inspection:
The surface quality of welds for visual inspection shall comply with class II I weld standard (GB50236-98), and the internal quality shall comply with class III weld standard (GB50236-98). The number of NDT for welds in general sections shall not be less than 20% of the total number of welds.
(9) For manual arc welding, the wind speed shall not exceed 8m / s, and the number of times of repairing the same part of the unqualified weld shall not exceed 2. During welding, a reasonable welding sequence shall be adopted, and the interlayer joints of multi-layer welding shall be staggered.
Pipeline excavation
1. The line shall be clearly marked on the road according to the drawing size and relevant regulations, and all sign lines must be double lines.
2. Mechanical trenching and manual trenching shall be used for earth excavation. Manual and careful operation shall be carried out at the location where the site is narrow or there are underground pipelines.
3. The earthwork is located in the south of the trench, and the operation site is located in the north of the trench.
4. The straight pipe trench shall be straight and smooth, and the curved pipe trench shall be smooth and excessive without concave convex and broken lines. The ditch wall and bottom shall be flat, and there shall be no collapse and sundries in the ditch.
5. When excavating the pipe trench, it is necessary to prevent rainwater from scouring the pipe trench. The excavation of each section of pipe trench shall be closely combined with pipeline assembly and welding and trench backfilling, and one section of excavation shall be completed in combination with medium and short-term weather forecast.
6. In the process of slotting, humus and residue need to be discarded, and the excess earthwork should be temporarily stored in a temporary storage yard near the site.
Electrofusion connection
1. Cut off the pipe with special tools, keep the end face of the pipe perpendicular to the pipe axis, scrape off its skin, scrape off half the length of the electric melting sleeve, and wipe the dirt on the connecting surface of the pipe and pipe fittings with clean cotton cloth
2. Draw a positioning line according to the insertion depth of the pipe, so as to ensure that the pipe can be equally inserted into the electric melting sleeve during assembly
3. Insert the pipe into the socket at one end of the electric melting sleeve to the positioning line, and check whether the inlet and outlet parts meet the requirements.
4. Install the sleeved pipe and electrofusion sleeve on the interface fixture and fix it with the fixture;
5. Fix the pipe at the other end on the fixture, push the fixture along the sliding shaft to insert it into the socket at the other end of the electric melting sleeve, and keep the two connecting pipes on the same axis.
6. Connect the wire plug of the controller with the electric fusion sleeve socket, correctly set the welding voltage, current, welding time and other parameters, open the electric fusion button of the controller, conduct electric fusion, and the welding time enters the countdown.
7. After the dissolution is completed, cool it to the ambient temperature according to the specified cooling time, and remove the fixture and electrofusion wire.
Pipe laying
1. Before the pipeline is laid into the trench, the trench bottom shall be measured to remove sundries, large soil blocks and ponding in the trench.
2. Special slings must be used for lowering the pipeline into the trench. It is strictly prohibited to damage the external anti-corrosion coating of the pipeline. It is strictly prohibited to lift the pipeline sharply or tighten the pipeline, resulting in bending or permanent bending. The spacing between lifting pipes is less than 20m.
3. After the pipeline is lowered to the groove bottom, it shall be close to the groove bottom and properly placed without external force. If there is any suspended part, it must be filled up.
Pipe backfilling
1. After the installation inspection of the main body of the pipeline is qualified, the trench shall be backfilled in time, but the installation interface that has not been inspected shall be reserved. Before backfilling, the sundries left at the bottom of the trench must be removed.
2. Garbage, wood and soft materials shall not be used for backfilling. The backfill on both sides of the pipeline and within 0.5m above the pipe top shall not contain debris such as gravel and bricks, and shall not be backfilled with lime soil. The stones in the backfill soil above 0.5m from the pipe top shall not be more than 10%, the diameter shall not be more than 0.1M, and shall be evenly distributed.
3. During trench backfilling, the partially suspended part of the pipe bottom shall be backfilled first, and then both sides of the pipe shall be backfilled.
4. The backfill soil shall be compacted in layers. The virtual paving thickness of each layer is 0.2-0.3m. The backfill soil on both sides of the pipeline and within 0.5m above the pipe top must be compacted manually. The backfill soil above 0.5m above the pipe top can be compacted by small machinery. The virtual paving thickness of each layer should be 0.25-0.4m.
5. After backfilling and compaction on both sides of the pipe and 0.5m above the pipe top, the support of the trench shall be removed under the condition of ensuring safety, and the gap shall be filled with fine sand.
6. After the backfill is compacted, the compactness shall be checked in layers, and the backfill records shall be made.
1. Before the installation of pipes, pipe fittings and valves, the model, specification and material shall be checked in detail to see whether they meet the design requirements, and the manufacturer’s product factory certificate and other quality assurance data shall be provided.
2. Before the installation of valves, the shell strength and tightness test shall be carried out one by one. The strength test pressure shall be the nominal pressure of the valve [1.5 times of the nominal pressure of the valve, the test medium shall be water, the pressure shall be maintained for 5 minutes, the test J shall be water, the pressure shall be maintained for 10 minutes, and the valve disc sealing surface shall be qualified if there is no leakage.
3. During pipe alignment, the flatness shall be checked and measured 200mm away from the interface center, and the allowable deviation shall not be greater than 1mm. Pay attention to the radian in the overall layout of the pipe group.
4. The pipe assembly clearance shall not be greater than 2mm, and the misalignment of the outer wall shall not be greater than 3mm, otherwise it shall be thinned and corrected.
5. During pipe connection, it is not allowed to use strong butt joint, or heat the pipe, add offset pad and other methods to eliminate the defects such as gap, deviation, staggered joint or non concentricity at the end face of the interface.
6. The flange connection shall be coaxial, the center deviation of the bolt hole shall not exceed 5% of the outer diameter of the hole, and the bolt shall penetrate freely, and the flange end face shall be parallel, the deviation shall not be greater than 1.5 ‰ of the outer diameter of the flange, and shall not be greater than 2mm, and the skew shall not be eliminated by tightening the bolt. All bolts shall be grade 8.8 strength bolts.
7. During installation, the safety distance between the gas pipeline and other adjacent pipelines and structures shall be strictly controlled, and the operation shall be carried out according to relevant operating procedures. The buried slope and depth must meet the design requirements.
8. For construction every other day, cast iron pipe shall be used to block the pipe orifice temporarily to prevent sewage, sundries and animals from entering the pipe.
9. The pipeline installation shall be inspected every 6-10m according to the inspection contents, and the next process can be carried out only after it is qualified.
Install the retaining bracket
1. During pipeline installation, the support shall be fixed and adjusted in time, the position of the support shall be accurate, the installation shall be flat and firm, and the contact with the pipeline shall be close.
2. The specification, type and installation position of the adopted support shall meet the design requirements, and the deviation of elevation and coordinate shall not exceed 10mm (there shall be no positive deviation of elevation).
3. The sliding surface of the guide support or sliding support shall be smooth and flat without jamming. The guide plate shall not affect the sliding of the pipe support. The fixed support shall be fixed firmly. The height of the vertical plate of the pipe support shall meet the requirements of the insulation thickness.
4. The support weld shall be fully welded. When welding with the pipe, the pipe wall shall be free of defects such as biting and burning through, and the welding shall be completed before the pipe system test.
5. After the installation of pipe support, check whether the specification, type, installation position, weld and bolt fastening meet the requirements of drawing design and construction specifications one by one, whether there is missing installation and whether they are in close contact with the pipe.
6. The overhead of low-pressure gas pipeline can be laid along the outer wall of buildings with fire resistance rating not lower than grade II.
7. The clear distance between the gas pipeline along the outer wall of the building and the door and window openings of the building: the low-pressure pipeline shall not be less than 0.3m.
Installation of valves and accessories
1. Check the packing before valve installation, and the gland bolt must have sufficient adjustment allowance.
2. Valves with flange or threaded connection shall be installed in the closed state.
3. Before installing the valve, the model shall be checked according to the design, and the installation direction shall be determined according to the gas flow direction.
4. The valve stem of the valve on the horizontal pipeline shall generally be installed within the upper half circumference.
5. When installing cast iron valves, avoid damage caused by strong connection or uneven stress.
6. The installation position of the valve shall not hinder the disassembly and maintenance of the equipment, pipeline and valve itself. The installation height of the valve shall be convenient for operation and maintenance. Generally, it is appropriate to be 1.2m away from the ground. When the valve is more than 1.8m away from the floor, it shall be centrally arranged and a fixed platform shall be set.
7. For valves on side-by-side pipelines, the clear distance between hand wheels shall not be less than 100mm. In order to reduce the pipeline spacing, valves arranged side-by-side shall be staggered.
8. The operating mechanism and transmission device of the valve shall be adjusted as necessary to make the action flexible and accurate.
Indoor pipeline installation
1. First install the pipe support according to the drawing and the actual situation, then install the processed pipe, and fix it after appropriate adjustment. If the floor has reserved the casing, install it according to the reserved position. If not reserved, the casing shall be added.
2. In order to ensure the installation quality, the riser installation shall be measured and installed with pendant and level.
3. The installation of buried pipeline at the entrance shall be constructed according to the slope requirements of the drawing of 0.02%, and polyethylene shall be strengthened for anti-corrosion treatment according to the requirements of the drawing.
4. There shall be no welded junction in the pipe passing through the floor casing.
5. The finished pipe orifice shall be bound with plastic cloth to prevent foreign matters from entering.
6. The straightness of horizontal pipeline for pipeline installation shall be 2L / 1000 and 3L / 1000 of riser.
7. The horizontal clear distance from indoor water supply, drainage and heating pipes shall not be less than 100mm, and the cross clear distance shall not be less than 10mm.
Gas meter installation
1. The gas meter must meet the following conditions before installation.
2. The gas meter has factory certificate, the manufacturer has production license, and the meter has been tested by legal testing unit;
3. It shall not exceed 4 months from the date of delivery. If it exceeds, it shall be tested by the legal testing unit;
4. No obvious damage. During the installation of gas meter, collision, inversion and knocking are not allowed, and rust, sundries and oil stain are not allowed to fall into the instrument.
5. The diaphragm meter must be installed flatly, and the lower part shall be supported. The horizontal clear distance between the gas meter and the surrounding facilities is listed in the following table.
Installation of surge tank
1. It shall be stated on the certificate of the pressure regulating box that it meets the requirements of the quality standard through the air pressure test, strength and tightness, as well as the adjustment of inlet and outlet pressure. Do not install without the above instructions.
2. When installing the surge tank, it shall meet the following requirements:
3. Before installation, check that the outer surface of the surge tank is free of defects such as sand sticking, sand holes and cracks;
4. The installation of the surge tank shall be flat and stable, and the inlet and outlet directions shall not be wrong;
5. The connecting pipe of the membrane of the surge tank and the connecting pipe of the commander shall be connected above the outlet pipe of the surge tank, and the length of the connecting pipe shall meet the actual requirements.
Overhead pipeline installation
1. The construction personnel shall be skilled and have high-altitude operation experience.
2. The lifting machinery used by the personnel shall be an electric basket (the disassembly and assembly of the basket must be operated by licensed professionals), and the lifting of pipes shall be a 2-ton electric crane. Walkie talkies shall be equipped on site to ensure clear signals and close cooperation among the commanders, overhead construction personnel, lifting machinery operators and ground assistance personnel.
3. Safety rope shall be set along the overhead construction pipeline. The safety rope shall be bound firmly and independently, and shall not be bound on the lifting machinery and basket support. A falling self-locking device is set on the safety rope. Overhead construction personnel shall wear safety helmets and safety belts. The connection between the safety belt and the self-locking device shall be reliable and firm.
4. Before the installation of the pipe support, the measurement shall be carried out to ensure the correct position of the support. The support installation must be flat and firm and in good contact with the pipe.
5. The overhead pipeline shall be prefabricated and derusted on the ground, and the first layer of yellow marking ready mixed paint shall be painted.
6. The prefabricated pipeline shall be hoisted to the installation position with hoisting machinery, fixed by personnel in a basket, and painted with the second layer of yellow marking ready mixed paint.
Construction of supporting facilities
1. Valve installation
When installing indoor steel valves, select corresponding connecting accessories according to the material of the pipeline, and be equipped with steel flanges, gaskets, bolts and other accessories of the same diameter. The flange surface and the valve flange shall be concentric and parallel, and the parallel deviation shall be 1.5% of the outer diameter of the flange and ≯ 2mm.
2. The specifications, dimensions and accuracy of bolts and nuts used in the project shall meet the requirements of drawings and GB97-81. The threads shall be complete, free of scars, thorns and other defects, and the bolts and nuts shall be well matched without looseness, jamming and other phenomena.
3. The installation position of the valve shall avoid the areas with dense and complex underground pipe network or heavy traffic as far as possible, and choose the place convenient for daily maintenance.
Pipeline purging
Pipeline purging is the same as general pipeline purging. Blasting purging can be carried out in sections. The medium is compressed air, and the pressure shall not exceed the working pressure of the pipeline.
Strength test
After removing the air in the pipeline, start the strength pressure test. The medium pressure gauge pressure is 0.6MPa and the low pressure is 0.2MPa. There is no pressure drop after stabilizing for 1h, and the inspection result is qualified.
Air tightness test
In the air tightness test, the medium pressure is 0.46mpa and the low pressure is 0.1MPa. It shall be maintained for a certain time to make the temperature of the test medium in the pipeline consistent with the ambient temperature of the pipeline. After the temperature and pressure are stable, the timing shall be started. The air tightness test shall be stabilized for 24 hours. If there is no obvious leakage or pressure drop, it will be qualified.
Handover acceptance
1. After the completion of all construction of the project, the handover acceptance shall be carried out, and the owner, the supervision unit and other relevant departments shall be notified to attend the handover.
2. The acceptance items mainly include strength, air tightness test, valve well and other aboveground facilities, which can be passed only after confirmation and signature.
3. The project acceptance shall be formally completed after the owner’s acceptance team and other departments issue the acceptance certificate.
4. For the delivery of completion data, the completion data shall include all contents in the completion data specified by the owner, and the owner shall issue the handover certificate of completion data.
Comments