Heat treatment: quenching medium
- Wilson Pipeline
- Jan 5, 2022
- 6 min read
What is quenching medium?
The medium used for quenching and cooling the workpiece is called quenching cooling medium (or quenching medium). The ideal quenching medium should have the condition that the workpiece can be quenched into martensite without causing too much quenching stress. This requires slow cooling above the “nose” of the C curve to reduce the thermal stress generated by rapid cooling; the cooling rate at the “nose” should be greater than the critical cooling rate to ensure that the undercooled austenite does not undergo non martensitic transformation; under the “nose”, especially when Ms points the temperature, the cooling rate should be as small as possible to reduce the stress of structural transformation.
The common quenchants are water, aqueous solution, mineral oil, molten salt, molten alkali, etc.
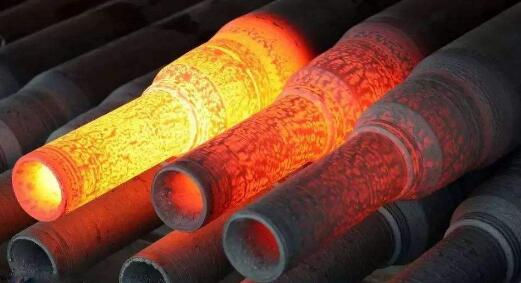
Water
Water is a quenching medium with strong cooling capacity. It has a wide range of sources, low price, stable composition and is not easy to deteriorate. The disadvantage is that in the “nose” region of C curve (about 500-600 ℃), water is in the steam film stage, and if it is not cooled fast enough, it will form a “soft point”; in the martensite transformation temperature region (300-100 ℃), water is in boiling stage, and cooling is too fast, which will easily cause martensite transformation speed to be too fast and produce great internal stress, resulting in deformation and even cracking of the workpiece. When the water temperature rises, there are more gases in the water or insoluble impurities (such as oil, soap, mud, etc.) in the water, the cooling capacity will be significantly reduced. Therefore, water is suitable for quenching and cooling of carbon steel workpieces with small section size and simple shape.
Saline and alkaline water
After the high temperature workpiece is immersed in the cooling medium by adding appropriate amount of salt and alkali in the water, the crystals of salt and alkali precipitate in the steam film stage and burst immediately. The steam film is destroyed and the oxide skin on the surface of the workpiece is also blasted. In this way, the cooling capacity of the medium in the high temperature region can be improved. Its disadvantage is that the medium is corrosive.
In general, the concentration of brine is 10% and that of caustic soda solution is 10% ~ 15%. It can be used as quenching medium for carbon steel and low alloy structural steel workpiece. The service temperature should not exceed 60 ℃. After quenching, it should be cleaned and antirust treated in time.
Oil
Mineral oil (mineral oil) is generally used as cooling medium. Such as oil, transformer oil and diesel oil. Generally, No. 10, No. 20 and No. 30 engine oils are used. The larger the oil number, the higher the viscosity, the higher the flash point, the lower the cooling capacity and the higher the service temperature.
At present, there are three kinds of new quenching oil: high speed quenching oil, bright quenching oil and vacuum quenching oil.
High speed quenching oil is a kind of quenching oil whose cooling rate is increased in high temperature region. There are two basic ways to obtain high-speed quenching oil. One is to select different types of mineral oil with different viscosity and mix them with appropriate ratio to improve the cooling capacity of high-temperature zone by increasing the characteristic temperature; the other is to add additives to ordinary quenching oil to form powdery ash like plankton in the oil. The additives are barium salt, sodium salt, calcium salt, phosphate, stearate, etc. The production practice shows that the cooling rate of high-speed quenching oil in the unstable region of undercooled austenite is obviously higher than that of ordinary quenching oil, while the cooling rate of high-speed quenching oil in low-temperature martensitic transformation zone is close to that of ordinary quenching oil. In this way, high hardenability and hardenability can be obtained, and deformation is greatly reduced. It is suitable for quenching alloy steel workpieces with complex shapes.
Bright quenching oil can keep the bright surface of workpiece after quenching. Bright quenching oils with different cooling rates can be obtained by adding polymer additives with different properties into mineral oil. The main component of these additives is brightener, which is used to suspend aging products insoluble in oil and prevent accumulation and precipitation on the workpiece. In addition, the additives of bright quenching oil also contain antioxidants, surfactants and refrigerants.
Vacuum quenching oil is a cooling medium for vacuum heat treatment and quenching. Vacuum quenching oil must have low saturated vapor pressure, high and stable cooling capacity, good brightness and thermal stability, otherwise the effect of vacuum heat treatment will be affected.
Salt bath and alkali bath quenchants are generally used in step quenching and isothermal quenching.
New quenchant
There are polyvinyl alcohol aqueous solution and three nitrate aqueous solution.
The co cooling capacity of polyvinyl alcohol (PVA) aqueous solution with mass fraction of 0.1% – 0.3% is between water and oil. When the workpiece is quenched into the solution, a layer of vapor film and a gel film are formed on the surface of the workpiece, and two layers of film are used to cool the heating workpiece. After entering the boiling stage, the film is broken and the workpiece cooling is accelerated. When the temperature reaches low, the PVA gel film is formed again, and the workpiece cooling rate decreases. Therefore, the solution has low cooling capacity in high and low temperature regions, high cooling capacity in the middle temperature zone and good cooling characteristics.
The Trinitro nitrate aqueous solution is composed of 25% sodium nitrate + 20% sodium nitrite + 20% potassium nitrate + 35% water. At high temperature (650 ~ 500 ℃), due to the precipitation of salt crystals and the formation of steam film, the cooling capacity is close to that of water. At low temperature (300-200 ℃), because of its high concentration, poor fluidity and cooling capacity close to that of oil, it can replace water oil double medium quenching.
Cooling method
The most widely used quenching classification in production practice is based on different cooling methods. There are mainly single liquid quenching, double liquid quenching, step quenching and isothermal quenching.
Single liquid quenching
It is a quenching operation method that the austenitic chemical parts are immersed in a certain kind of quenching medium and cooled to room temperature. Single liquid quenching medium includes water, brine, alkali water, oil and specially prepared quenchant. In general, carbon steel is quenched and alloy steel is quenched with oil.
The operation of single liquid quenching is simple, which is conducive to the realization of mechanization and automation. Its disadvantage is that the cooling rate is limited by the cooling characteristics of the medium, which affects the quenching quality. For carbon steel, single liquid quenching is only suitable for the workpiece with simple shape.
Double liquid quenching
It is to immerse the austenitic chemical parts into a medium with strong cooling capacity, take out the steel parts before reaching the quenching medium temperature, and immediately immerse them in another medium with weak cooling capacity for cooling, such as water before oil, water before air, etc. Double liquid quenching can reduce the tendency of deformation and cracking. The operation is not easy to master, so it has some limitations in application.
Martensite step quenching
It is a quenching process in which the austenitic chemical parts are immersed in the liquid medium (salt bath or alkali bath) with the temperature slightly higher or lower than the martensitic point of the steel for a proper time. After the inner and outer layers of the steel parts reach the medium temperature, they are taken out for air cooling to obtain the martensitic structure, which is also called graded quenching.
The results show that the staged quenching can effectively reduce the phase transformation stress and thermal stress, and reduce the quenching deformation and cracking tendency because the staged temperature stays at the same internal and external temperature of the workpiece. Step quenching is suitable for alloy steel and high alloy steel workpieces with high deformation requirements, and can also be used for carbon steel workpieces with small section size and complex shape.
Bainite austempering
It is a quenching process, sometimes called austempering, in which steel parts are austenitized and rapidly cooled to the bainite transformation temperature range (260-400 ℃) and kept isothermal to transform austenite into bainite. The general holding time is 30-60min.
Compound quenching
The workpiece is quenched below MS to obtain 10% – 20% martensite, and then isothermal in the lower bainite temperature region. The results show that the M + B structure can be obtained by this cooling method. The martensite formed during pre quenching can promote bainite transformation and temper martensite at isothermal temperature. Compound quenching can avoid the first kind of temper brittleness and reduce the residual austenite volume, that is, the tendency of deformation and cracking.
Special parts are also compressed air quenching, spray quenching and jet quenching.
Source: China Pipe Fitting Manufacturer – wilsonpipeline Pipe Industry Co., Limited (www.wilsonpipeline.com)
(wilsonpipeline Pipe Industry is a leading manufacturer and supplier of nickel alloy and stainless steel products, including Super Duplex Stainless Steel Flanges, Stainless Steel Flanges, Stainless Steel Pipe Fittings, Stainless Steel Pipe. wilsonpipeline products are widely used in Shipbuilding, Nuclear power, Marine engineering, Petroleum, Chemical, Mining, Sewage treatment, Natural gas and Pressure vessels and other industries.)
If you want to have more information about the article or you want to share your opinion with us, contact us at sales@wilsonpipeline.com
Comments