Failure Analysis of Flange Crack
- Wilson Pipeline
- Jan 5, 2022
- 5 min read
Abstract:There were many radial cracks on the stainless steel flange surface after storing for five years in Nibo. Marco and micro observation, chemical composition analysis and metallurgical examination were carried out to find out the failure cause. The results show that the fracture mode is stress corrosion. The material of the flange is 1Cr17Ni7, but the not required material: 304. The corrosion resistance of 1Cr17Ni7 is poorer than that of 304. In addition, the carbide network along the grain boundaries in the 1Cr17Ni7 promoted the occurrence of stress corrosion. Key words: flange stainless steel stress corrosion carbide network
Introduction
Flanges are generally used for parts transfer to facilitate disassembly and assembly. Flange pairs are fastened together by bolts. Pipe flange materials generally use Q235, equipment flange materials generally use 20 steel, 16Mn, 304, 316, 316L. In order to investigate the impact of the storage environment on the engine, the engine was stored in a relatively harsh and high temperature and humid South Coast. After 5 years, the inspection found that there was a serious corrosion phenomenon in the exit flanges of the 20 equipment, of which 14 equipment outlet flanges were cracking at the same time. The material used for the cracked flange is 304 stainless steel. Because of its excellent mechanical properties and corrosion resistance, the stainless steel is widely used in various corrosive environments, especially in the harsh marine environment, but the corrosion of stainless steel components and parts for a long time in this corrosive environment is not possible. In addition to the common influence of stress and corrosion, the stainless steel material will have serious stress corrosion cracking in addition to uniform corrosion, which has great destructiveness. The two major factors affecting the stress corrosion of stainless steel are internal and external factors: internal factors mainly include material composition and tissue state, and the external factors mainly include the use environment (corrosion medium concentration, temperature) and the stress state of their own. Through analyzing the causes of flange cracking, we find out the main causes of stress corrosion, and provide technical support for product storage and life extension at sea.
1 Test process and analysis
Observation of 1.1 cracks and observation of crack section
The macroscopic morphology of the cracked flange is shown in Figure 1. There is a serious corrosion phenomenon on the surface of the flange. 8 radial cracks are visible on the visual surface, and the cracks are not penetrable to the wall thickness. The 8 cracks are evenly distributed in the circumference, and each crack is composed of multiple intermittent cracks.
Figure 1 crack macroscopic morphology
Mechanical method was used to open the cracks. The cracks were uneven and the red rust was attached to the cross section. The artificial section was bright metallic color (Fig. 2).
Figure 2 fracture macroscopic morphology
After cleaning the section, the morphology observation and energy spectrum analysis are carried out under scanning electron microscope. The whole crack section is along the crystal morphology, the two cracks are visible along the crystal, and a layer of corrosion product is attached to the crystal surface. The energy spectrum analysis of the corrosion products mainly contains O, Fe, Cr and the S and Cl elements with high content; the artificial cross section is dimple. Morphology, energy spectrum analysis mainly contains Fe, Cr (19%), Ni (7.1%), Si (1%), Mn (1.9%) elements (all mass fraction). The fracture micromorphology is shown in Figure 3. The fracture characteristics above show that the cracking property of the flange is brittle fracture.
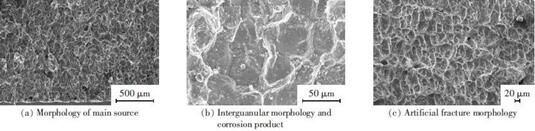
Figure 3 fracture micromorphology
1.2 metallographic analysis and microhardness test
After sampling and preparing the metallographic specimens near the parallel cracks, there are many basic radial cracks on the specimen (Fig. 4).
Figure 4 crack morphology After etching the metallographic sample, it is observed that 1) the cracks are all along the crystal growth; 2) the grain size of the matrix is not uniform, the grain size is larger (GB/T 6394 – 2002 more than 00 stages), some grain is relatively small (8.5 grade), and the large grain region and the small grain area are spaced distribution; 3) the granular carbide in the grain boundary is distributed in the grain boundary. The hardness of the samples was tested as HV0.2 234, 235, 245, 237 and 250, with an average value of HV0.2 240, equivalent to HRC 20.5.
1.3 chemical composition analysis
The sample and chemical method are tested on the flange, and the results show that the grade of the material used in the flange does not conform to the requirements of 304 stainless steel (equivalent to the domestic brand 0Cr18Ni9), which is in accordance with the 1Cr17Ni7, and the test results are detailed in Table 1.
Figure 5 flanged microstructure
Table 1 results of material composition analysis (mass fraction /%)
2 Analysis and discussion
After the export flange is installed on the equipment, it has been parking in Ningbo for 5 years. It is found that there are cracking phenomena in 14 outlet flanges of 20 sets of equipment export flanges. It is found that there is a serious corrosion phenomenon on the surface of one of the flanges, and 8 obvious radial cracks are visible, and each crack is composed of a number of intermittent small cracks. The fracture fracture observation shows that the crack section is uneven, the cross section adheres to the reddish brown corrosion product, the microstructure is along the crystal morphology, and a layer of matrix corrosion product is attached to the crystal surface, and the corrosion products contain high corrosive medium S and Cl elements. The fracture characteristics above show that the cracking property of the flange is brittle crack, and the cracking mechanism is stress corrosion. The results of chemical analysis show that the material used for flanges is 1Cr17Ni7, which does not meet the requirements of design brand 304 (0Cr18Ni9). Compared with 304, 1Cr17Ni7 is high in C content and low in Cr and Ni content, resulting in low corrosion resistance (uniform corrosion and intergranular corrosion). The results of metallographic analysis show that the cracks are all intergranular, the grain size is uneven, and there are intergranular carbide grains. The precipitation of a large number of carbide leads to the decrease of [1 – 3] in the grain boundary Cr content. The electrode potential of poor Cr region is lower than that in the crystal. Under the action of corrosion medium, the grain boundary of low electrode potential becomes anodic and is corroded, resulting in the decrease of the intergranular corrosion resistance of the material [4 – 8]. The comprehensive analysis shows that the cracking mode of the flange is stress corrosion, and the cause of stress corrosion is related to the following two factors: 1) the material used in the flange does not meet the design requirements, and the 1Cr17Ni7 material is used instead of 304 stainless steel, while the corrosion resistance and intergranular corrosion properties of the 1Cr17Ni7 material are all worse than that of the 304 stainless steel; 2) 1Cr17Ni7 matrix group Weave the intergranular carbide in the intergranular distribution, resulting in the decrease of grain boundary corrosion resistance of the material.
3 Conclusion
The cracking mode of the flange is stress corrosion.
The cause of stress corrosion in the flange is that the flange used 1Cr17Ni7 instead of the design requirements of 304 stainless steel, and the 1Cr17Ni7 matrix has a reticulate carbide along the crystal, which leads to the decrease of the corrosion resistance of the material.
Author: Wang Ying, Xie Guojun, Han Lu, Pang Jincheng wilsonpipeline.com is a professional stainless steel flange manufacturer, producing stainless steel flanges of super double phase stainless steel, double phase stainless steel, alloy steel, stainless steel and so on. Source: China Stainless Steel Flange Manufacturer – wilsonpipeline Pipe Industry Co., Limited (www.wilsonpipeline.com) Reference [1] Arutunow A, Darowicki K, Zielinski A. Atomic force mi-croscopy based approach. 2011, 56 (5). [2] Dai Yongxiang, Lian Fang, Li Ji, et al. Study on intergranular corrosion behavior of 304 stainless steel [J]. light automobile technology, 2011 (5/6): 34-37. [3] Bi Hong Yun. Grain boundary engineering inhibits chromium depleted grain boundary of SUS304 stainless steel [J]. steel, 2005, 40 (6): 68-71. [4] Ye Chen Qing, Hu Rong Gang, Hou Ruiqing, et al. Scanning micro electrode method for sensitizing treatment of localized corrosion behavior of 304 stainless steel. [J]. electrochemistry, 2013, 19 (6): 507-510. [5] Jin Guangxi, Pu Meishan. Failure analysis of stress corrosion cracking of 304 stainless steel heads [J]. hot working technology, 2011, 40 (23): 226-228. [6] Hu Xiaohui 1Cr18Ni9 stainless steel clamping strip fracture analysis, [J]. failure analysis and prevention, 2008, 3 (3): 55-58. [7] Zhang Xinming, Feng Jijun, Lu Liulin, et al. Cracking failure analysis of stainless steel welded joint of thermoregulant [J]. failure analysis and prevention, 2014, 9 (6): 368-374. [8] Jiang Tao, Yu Yang, Yang Sheng, et al. Discussion on stress corrosion problems of stainless steel from failure cases. [J]. corrosion and protection, 2011, 32 (4): 297-300. [9] Wang Ying, Xie Guojun, Han Lu, Jin Cheng. Analysis of flange cracking cause [J]. failure analysis and prevention, 2016, 11 (6): 369-371.
Comments