Discussion on anti-corrosion materials for flange equipment
- Wilson Pipeline
- Jan 5, 2022
- 5 min read
Flange is the main connecting equipment of process pipeline in petrochemical enterprises. It has a large number and plays a very important role in production and operation. Most of Fujian coastal petrochemical enterprises are located in coastal areas. The high salt and high humidity marine corrosive atmosphere accelerates the corrosion rate of station flanges, resulting in a wide range of flange corrosion, especially flange clearance and flange gasket corrosion, which will not only cause equipment damage and shorten service life, but also cause management medium leakage, and bring great potential safety hazards to production safety.
Flange corrosion mechanism
By analyzing the mechanism of flange corrosion, there are mainly the following:
The flange clearance space is narrow (the common flange clearance size is about 2 ~ 20mm, which is easy to accumulate dust and salt in the air, which are the inducing factors of corrosion and will lead to rapid corrosion;
The flange has a gap structure, which is a typical structure of crevice corrosion and a prerequisite for the formation of crevice corrosion. A narrow flange gap will cause different oxygen concentrations inside and outside the gap, forming an oxygen concentration difference battery, greatly accelerating the occurrence of corrosion;
Some petrochemical enterprises are located in coastal areas. The coastal air is high in humidity and salt. The water, gas and salt rich in the air are very easy to damage the flange coating and cause local corrosion;
In the design stage, attention is not paid to the anti-corrosion part or anti-corrosion structure design, resulting in the connection of flange surfaces of different materials and the selection of metal gaskets with different materials from the flange surface during construction, resulting in galvanic corrosion.
Flange anti-corrosion method
The most appropriate anti-corrosion process shall be selected according to the corrosion environment and corrosion severity of the flange. The details are as follows:
The anti-corrosion design avoids the design of narrow gap structure, resulting in gap corrosion and impurity accumulation, and the same metal is designed for the same flange surface to avoid galvanic corrosion;
Strengthen the construction quality control during construction and strictly control the substrate bottom;
Treatment and coating construction quality;
Consider using non-metallic gaskets to reduce the probability of galvanic corrosion of gaskets. If sacrificial anode protection is provided, consider flange bridging;
The new coating anti-corrosion process is adopted, and the coating material with excellent anti-corrosion performance is selected to completely fill and cover the flange gap, isolate the corrosion sources such as water, air and impurities, and contact the inner surface and gasket of the flange gap, so as to realize long-term anti-corrosion.
The flange is coated with anti-corrosion materials
In the case that the traditional coating anti-corrosion can not effectively prevent the flange from corrosion, through investigation, a variety of new coating materials are selected and tested on the flange, and their anti-corrosion processes are tested and improved. Some flange coating anti-corrosion processes have achieved good anti-corrosion effects.
Wax magnetic anti-corrosion material is an excellent anti-corrosion protection material. Wax Tape anti-corrosion material mainly includes wax tape and wax magnetic primer, which can well isolate water and air. It can be applied to the anti-corrosion of various irregular pipelines, valves, flanges, bolts and other equipment in various corrosive environments. In 2006, NACE formulated the standards related to wax magnetic anti-corrosion materials.
Viscoelastic anti-corrosion material is a new type of high molecular polymer anti-corrosion material originated in the Netherlands. Its state is between liquid and solid. At room temperature, it can remain in a state of no flow and no solidification for a long time. In addition, viscoelastic has very good bonding performance, waterproof and air isolation performance.
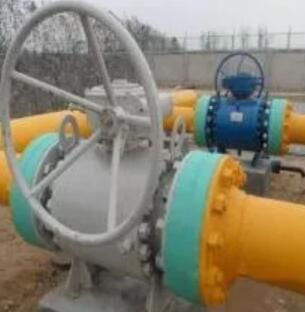
According to the experience of equipment anti-corrosion maintenance in many petrochemical enterprises along the coast of Fujian, the traditional coating anti-corrosion can not meet the increasingly severe demand for station flange anti-corrosion. According to the characteristics of coastal and long-term marine corrosive atmosphere with high humidity and high salt, the disadvantages of the traditional coating anti-corrosion method are analyzed, and two coating anti-corrosion materials with excellent anti-corrosion performance are selected to be used in Fujian After several years of experience accumulation, it is considered that the wax magnetic anti-corrosion material and viscoelastic anti-corrosion material have good applicability and good anti-corrosion effect on the process flange equipment of petrochemical enterprises.
Several solutions to flange corrosion
The integrity of the flange connection is very important for the fluid piping system. Since the sealing surface of the flange connection can only be visually inspected when the whole system is closed, the inspection process should be as simple as possible. First, external corrosion should be eliminated. If it cannot be stopped, only ultrasonic technology can be used for detection. If external corrosion cannot be controlled, the process will be more complex and cannot be controlled Therefore, in order to monitor the whole system and provide effective and feasible quality control and maintenance procedures, the external corrosion protection of flanges and fasteners is very important.
The ideal solution should take into account excellent corrosion resistance and simple construction procedures. It is suitable for flanges of various sizes and shapes. It is easy to operate bolts during maintenance. At present, the following solutions are commonly used in the market.
1. Maintenance paint solution
Maintenance paint is a hard film that can be directly bonded to the substrate, usually epoxy or polyurethane paint. The flange has many corners and edges. Due to the effect of edge thinning, it is difficult for the traditional coating system to effectively cover the edge. Although the thickened coating can solve the problem of edge protection, it will seal the fasteners and cannot be removed for future maintenance.
2. Mechanical solutions
The gap between flange and flange surface is mainly sealed by protective cover, usually made of stainless steel or plastic clamp, and equipped with rubber sealing strip. This protection method is not flexible, and it is necessary to store covers or fixing devices that fully match flanges of various sizes.
3. Tape or semi-solid anti-corrosion tape solution
Roll packaged tape (such as Vaseline tape, wax tape or elastic polymer bandage) is protected by winding on the surface of the substrate. Since the semi-solid polymer is waterproof, this protection method can provide reliable protection. However, if the flange shape is complex, this material is not only time-consuming, but also difficult to construct.
4. Hot melt plastic solutions
Hot melt plastic is essentially a waxy fusible polymer heated at high temperature, which can be sprayed on the substrate surface through professional hot melt equipment. The advantage of this protection method is that it can be remelted and reused, saving cost. However, although it can be reused, it still needs hot work, professional equipment and construction services, but it is not easy to open and close during maintenance Seal.
5. Polymer sealed bag solution
The sealing bag can completely cover the flange. Its composition is composed of low permeability polymer, corrosion inhibitor steam and desiccant. It is easy to install, but the two ends of the bag are only sealed with tape instead of long-term effective mechanical bonding. The steam space has a large area, it is easy to accumulate a large amount of water, and the corrosion inhibitor will be consumed over a period of time.
Source: China Flanges Manufacturer – wilsonpipeline Pipe Industry Co., Limited (www.wilsonpipeline.com)
Comentarios