Corrosion and protection of buried pipelines
- Wilson Pipeline
- Jan 5, 2022
- 8 min read
With the development of the national economy, the advantages of buried pipelines are increasingly recognized by the public. At the same time, the problems caused by the leakage of buried pipelines are increasingly concerned by the public. Therefore, the preservation of buried pipelines has become an important issue. .
1. Buried pipeline and laying environment
Here we say that buried pipelines are specifically metal pipes, and considering the prevalence of use in water supply and drainage projects, we have chosen two metal pipes for discussion, one is ductile iron pipe and the other is carbon steel pipe.
In most cases, buried pipelines are laid in the topsoil. The average person would think that the soil is a granular solid, but in fact, when we conducted related research, we thought that the soil is a three-phase system of solid, liquid and gas, and the latter two played a crucial role. Among them, solid materials include soil minerals, organic matter and microorganisms, and liquids and gases exist in the pores of soil particles. The soil can be pided into sandy soil, clay soil and loam. Among them, the sandy soil has many sediments, coarse particles, fast water seepage, poor water retention performance, good aeration performance, and slime. The nature of the soil is exactly the opposite of sandy soil, and the nature of the loam is middle. Pipes are buried in soils of different natures, and the degree of corrosion is different.
In fact, in many cases, a pipe needs to be in contact with soil of different nature, and the different physicochemical properties of the pipe surface are likely to lead to increased corrosion of the pipe. Therefore, in this case, anticorrosion construction should be better. jobs.
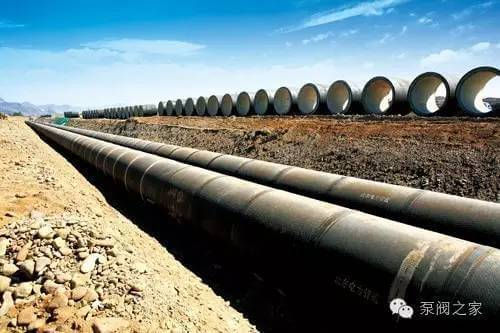
2. Types of corrosion of buried pipelines and introduction
Metal corrosion is pided into chemical corrosion (specifically non-electrochemical corrosion) and electrochemical corrosion. Among them, the latter accounted for the vast majority. Electrochemical reactions are a branch of a chemical reaction that must have the presence of a metal as an electrode, an electrolyte as a reaction environment, and a conductive loop. Most of the corrosion of buried pipelines is caused by electrochemical reactions.
There are many types of buried pipeline corrosion, including galvanic corrosion, concentration battery corrosion, pitting, pitting and so on. Here, we focus on three common forms of corrosion, galvanic corrosion, concentration cell corrosion, and microbial corrosion.
2.1 galvanic corrosion
Primary batteries are the most basic form of electrochemical reactions and are often used in situations where electrochemical reactions are introduced. The picture below is a schematic diagram of a primary battery.

In the figure, copper and zinc are respectively used as the two poles of the battery, the two poles are immersed in the same electrolyte solution, and the wires are connected to the two poles.
When the two poles are connected by wires, due to the different properties of the two metals, zinc is more active than copper, and a potential difference is generated. The zinc as the positive electrode of the primary battery loses electrons, and the copper of the negative electrode acquires electrons. As a result, the corrosion of the zinc electrode is intensified, and the corrosion of the copper electrode is slowed down or even stagnated.
The greater the potential difference between the two metals separated in the potential sequence, the stronger the corrosion, so the two metals in the potential sequence that are far apart should not be connected together. In fact, the primary battery is more like a double-edged sword. This principle is often used in engineering to slow the corrosion of steel pipes.
In actual operation, there are several points to note. One is to replace a pipe. When a pipe is replaced due to corrosion damage, if it is not noticed, the new pipe segment will often fail quickly. Because the new pipe section is an anode, it tends to be short, while the old pipe section is a cathode, which is often long. A small section of new pipe needs to supply several times its own old pipe section, and its corrosion rate will be much greater than the corrosion rate of its own buried ground. There is also a weld of the pipe. The metal body of the steel pipe and the metal composition of the weld are different. The potential difference between the two can reach 0.275V. Therefore, the adjacent portion of the weld with low potential after being buried in the ground is easily corroded. . Therefore, in the above circumstances, we should do a good job in anti-corrosion work.
2.2 Concentration battery corrosion
Concentration batteries are quite common in the corrosion of buried pipelines, which are pided into metal ion concentration difference batteries and oxygen concentration difference batteries.
Concentration batteries are also essentially caused by the difference in metal potential between the two poles. The metal ion concentration battery is because the concentration of metal ions in the electrolyte where the two poles are different, and the oxygen concentration battery, as the name suggests, is because of the electrolyte solution where the two poles are located. Caused by different oxygen concentrations.
Among them, oxygen concentration batteries are most common in buried pipeline corrosion. This has a lot to do with different soil properties. The concentration of oxygen in different parts of the pipeline is different. The natural potential (non-equilibrium potential) of the pipeline in the oxygen-depleted part is low, which is the anode of the corrosion original battery. The anode dissolution rate is obviously higher than the anode dissolution rate of the remaining surface, so it suffers from corrosion. The pipeline passes through the soil junction of different natures. The clay section is depleted of oxygen and is prone to corrosion, especially at the junction of the two soils or the location of the buried pipeline near the excavation end.
In actual operation, the buried pipelines are often in different tamping layers, the pores of the soil are different, and the oxygen holding capacity naturally differs, which provides conditions for the formation of oxygen concentration batteries.
2.3 Microbial corrosion
Microbial corrosion is essentially bacterial corrosion, which is also an electrochemical corrosion in nature, except that the medium changes the physical and chemical properties of the interface of the material it contacts due to the propagation and metabolism of the corrosive microorganisms.
There are many types of bacteria involved in bacterial corrosion, and the most harmful one is sulfate-reducing bacteria (SRB). Sulfate-reducing bacteria are bacteria that use organic matter as a nutrient to reduce sulfate to sulfide under anaerobic conditions. SRB is an anaerobic bacterium that needs to grow under anaerobic conditions and actually multiplies rapidly in a local anaerobic environment.
Von Wogozen Kuhr et al. proposed a classical depolarization theory in 1974. It is believed that pitting corrosion of buried cast iron pipes is due to the activity of SBR to deoxidize the metal surface by hydrogenase. The overall reaction formula is as follows:
4Fe + SO42- + 4H2O ==3Fe(OH)2 + FeS + 2OH-

3. Anti-corrosion of buried pipelines
In view of the corrosion principle and process described above, the anticorrosion means of the buried pipeline in the project is mainly pided into three aspects, external application, lining and cathodic protection. Among them, the external application mainly includes asphalt, galvanized, PE tape, etc., the inner lining mainly includes resin, cement mortar, plastic, etc., and the cathodic protection is also pided into two kinds of DC power supply and no DC power supply.
Next, we introduce the anti-corrosion measures for ductile iron pipes and carbon steel pipes.
3.1 ductile iron pipe
In terms of material properties, the anti-corrosion performance of ductile iron pipes is better than that of carbon steel pipes. Therefore, it has been widely used in the field of buried pipeline transportation. At present, the ductile iron pipe adopts the cement lining as the internal anti-corrosion form, the zinc layer plus the asphalt as the external anti-corrosion form, and has been completed in the production process, and the anti-corrosion treatment is not required after the construction and installation. This has become a common practice for spheroidal graphite cast iron pipe manufacturers at home and abroad, and is suitable for most soil types. It has been proved by practice that the anti-corrosion effect is also very obvious.
Among them, it is important to point out the importance of the zinc layer as a means of external preservation.
First, electrochemical protection
The potential of iron is -0.440 mV, and the potential of zinc is -0.763 mV, which is lower than the potential of iron, and the potential of oxygen is 1.4 mV. Thus, the potential difference between the zinc and oxygen is large, and the primary battery is more easily formed, thereby protecting the cast iron pipe wall.
Second, form a stable protective layer
Once the asphalt coating on the surface of the zinc layer is destroyed, the zinc layer is in contact with the soil, and the metal zinc combines with carbonates in the soil to form insoluble zinc carbonate, which is tightly bonded to the tube wall. Forms a dense, continuous, insoluble, non-leakable coating to prevent corrosion.
Third, the self-healing of the damage
Local damage may occur during pipeline transportation or installation. Zinc is rapidly converted to zinc ions by the action of the primary battery. Zinc ions migrate through the pores of the asphalt layer to seal the pores and cover the damage, forming a stable and insoluble protective zinc layer.
In addition, the zinc layer and the asphalt have excellent adhesion, which is essential in corrosion protection.
3.2 carbon steel pipeline
The corrosion resistance of carbon steel pipes is poor, but because of its high pressure resistance and good processability, it has also been widely used in buried pipelines.Therefore, its anti-corrosion practice has become the focus of the project.
At present, the technologies used for external corrosion protection of buried steel pipes mainly include petroleum asphalt anti-corrosion layer, coal coke-stained porcelain anti-corrosion layer, polyethylene adhesive tape anti-corrosion layer, sintered epoxy powder anti-corrosion layer, and two-layer structure polyethylene anti-corrosion layer. Three-layer structure polyolefin anti-corrosion layer technology.
Here, we mainly introduce the polyethylene adhesive tape anti-corrosion layer technology.
The polyethylene adhesive tape anticorrosive system consists of a primer, an inner anticorrosive tape and an outer protective tape. The anti-corrosion layer is pided into different grades. According to different pipe diameters, environment, anti-corrosion requirements and construction conditions, different anti-corrosion layer structure and thickness are selected.
Polyethylene adhesive tape anti-corrosion layer has excellent water resistance and oxidation resistance, low moisture absorption rate, good insulation, anti-cathode peeling, impact resistance, wide temperature range, stable performance in the temperature range of 30~80 °C. The anti-corrosion quality of polyethylene adhesive tape mainly depends on the adhesion of the adhesive film interface. The non-solvent adhesive is used to bond the polyethylene-based film and the solvent-free adhesive under heat under a certain pressure to make the polyethylene adhesive tape strong and stable, and the quality of the anti-corrosion layer is obtained. Guarantee.
The main disadvantage of the polyethylene adhesive tape anti-corrosion layer is that it has poor resistance to soil stress, especially at high temperatures, resulting in cathode shielding due to poor adhesion and compactness.
3.3 Cathodic protection
Cathodic protection is an anti-corrosion method for protecting the outer wall of a buried pipeline according to the principle of the original battery. According to the principle of the original battery, only the anode of the two electrodes is corroded. Therefore, the cathodic protection is to make the metal pipe become a cathode by artificial means to prevent corrosion.
There are two types of cathodic protection, one is cathodic protection without external current. The specific method is to use a metal material (active) that is more reductive than steel, such as magnesium, zinc, etc. as an anode, and bury it in the ground, connect the anode to the pipeline with a wire at a certain distance, and naturally form a large one in the soil. The result of the circuit is that the anode metal is corroded and the steel or cast iron pipes are protected. This method is often used in situations where soil resistivity is low, power is not available, and pipe coating is good.
There is also a cathodic protection method that applies DC power. The specific method is: burying scrap iron or the like in the vicinity of the metal pipe, as an anode, connecting with the anode of the direct current, and the cathode of the power source is connected to the pipeline. The current flows from the DC power source through the cable to the artificial scrap iron anode, and then flows into the protected pipeline through the soil, and flows from the pipeline back to the cathode of the power supply through the cable, so that the protected pipeline becomes a cathode, thereby preventing soil corrosion of the pipeline.This method is more suitable when the soil resistivity is high or the metal pipe is exposed.
In fact, cathodic protection is often used in conjunction with the outer coating of the pipe to achieve better corrosion protection.
Source: China Steel Pipelines Manufacturer – wilsonpipeline Pipe Industry Co., Limited (www.wilsonpipeline.com)
Comments